Modular home cost is a significant consideration for prospective homeowners. At HOW.EDU.VN, we provide expert insights into understanding the expenses involved in building a modular home and offer tailored solutions to meet your budgetary needs. Explore the world of prefab construction costs, modular building prices, and manufactured home expenses with our guidance.
1. Understanding the Basics of Modular Home Costs
Modular homes are constructed in a factory setting and then transported to the building site for assembly. This process often leads to cost savings compared to traditional stick-built homes. However, the final modular home cost can vary widely based on several factors.
1.1. Key Factors Influencing Modular Home Cost
- Size and Floor Plan: Larger homes and more complex floor plans will generally cost more.
- Customization: The level of customization you desire will significantly impact the price.
- Materials and Finishes: The quality of materials and finishes you choose will affect the overall cost.
- Location: Building costs can vary significantly depending on your geographic location.
- Contractor Fees: The fees charged by your general contractor will play a role in the final price.
- Land Development: Costs associated with preparing the land, including utilities and foundation work.
1.2. Breaking Down the Costs: Home-Only vs. Turn-Key
Understanding the difference between “Home-Only” and “Turn-Key” prices is crucial for budgeting.
- Home-Only Price: This includes the cost of the modular home itself, built to standard specifications and ready for delivery from the factory. It does not include delivery, installation, or site preparation costs.
- Turn-Key Price: This is a comprehensive price that includes everything from the Home-Only cost to delivery, installation, foundation work, utility connections, and interior/exterior finishing.
2. Detailed Cost Breakdown for Modular Homes
To provide a clearer picture of modular home cost, let’s examine the various expenses you might encounter. These figures are ballpark estimates and can vary based on location and specific project requirements.
2.1. Foundation Costs
A solid foundation is essential for any home. For modular homes, you typically have two options: a basement or a crawlspace. A slab foundation is generally not an option for modular construction.
- Basement: A poured basement with 8-foot walls, an egress window, insulation, and stairs can range from $35,000 to $40,000 for a 1,600 SF ranch home. This includes excavation, backfill, footers, walls, waterproofing, a sump pit, drain tile, the basement floor, sill plates, and an egress window.
- Crawlspace: A block crawlspace that is around 4’ deep, including an access panel and foam board insulation, typically costs between $18,000 to $20,000 for a 1,600 SF ranch home. This includes excavation, backfill, footers, walls, damp proofing, a sump pit, drain tile, sill plates, and an access door.
2.2. HVAC System Costs
A complete HVAC system is necessary for heating and cooling your modular home.
- HVAC System: Installing a full HVAC system, including the furnace, AC, air ducts, and gas lines, generally costs between $10,000 and $15,000 for a 1,600 SF ranch home. Some modular home packages include the furnace, but the AC unit will typically need to be installed on-site.
2.3. Garage Costs
Adding a garage can increase the value and functionality of your modular home.
- Garage: A simple 22X22 attached garage, including the garage door and opener, siding, roofing, and concrete work, can add between $23,000 and $25,000 to your modular home cost.
2.4. Water and Sewer Connection Costs
Access to water and sewer services is critical. Your options depend on whether you’re in a city or a rural area.
- Well: A drilled well that is 60 feet deep, including the bladder tank and water line hookups to the home, can cost between $5,000 and $7,000.
- City Water Hookup: City water costs vary considerably depending on location and tap-in fees. Contact your local water company for specific charges.
- Septic System: A standard in-ground septic system with a single tank and leach field in good soil typically costs between $7,000 and $9,000.
- City Sewer Connection: City sewer connection costs also vary. Contact the city building department to inquire about sewer tap fees. For areas outside city limits with unsuitable soil, a mound septic system may be required, with costs varying depending on soil conditions and the size of the mound.
2.5. Electrical and Gas Service Costs
Setting up electrical and gas services involves several components.
- Electrical Service: Installing an electric meter base on the home and running the line from the outside meter base into your home’s electric panel typically costs between $4,000 and $6,000. This includes miscellaneous electrical work needed per code requirements.
- Gas Service: Hookup to the local gas service may require a deposit or fee. The gas utility company will usually run the lines to your home and install a gas meter for free, depending on the distance. Propane tank installation involves a set fee for the tank, line, and pressure reducing valves, plus the cost of propane.
2.6. Building Permits
Like stick-built homes, modular homes require building permits.
- Building Permits: Total permit costs can fluctuate from $500 to as high as $4,000, with an average around $1,200. The costs are determined by local ordinances and the size of the home.
2.7. Driveway Costs
A driveway is often a necessary feature, and the cost depends on the material used.
- Driveway: Concrete work typically costs $5 to $6 per square foot for a 4” thick drive. A 10’ wide gravel drive can cost $6 to $8 per running foot.
2.8. Miscellaneous Charges
Other costs to consider include general contractor fees, gutters, lawn grading, and more.
- Miscellaneous: These charges can include delivery and setting, interior and exterior finish work, gutters, construction drive, permits, survey/home pinning, sidewalks, dumpsters, exterior steps, and general contractor site management fees.
3. Sample Modular Home Cost Estimate
To illustrate the potential costs, here’s a sample bid for a 1,493 SF ranch home, based on the Cedar Forest Ranch model.
Item | Cost |
---|---|
Ranch Home (1,493 sq. ft.) | $132,682 |
Foundation: Poured Basement | $38,769 |
HVAC | $9,500 |
Private Well | $5,500 |
Standard In-Ground Septic System | $7,500 |
PVC Drains & Plumbing | $5,100 |
Electrical Service | $5,800 |
Miscellaneous | $38,900 |
Total Price | $243,751 |
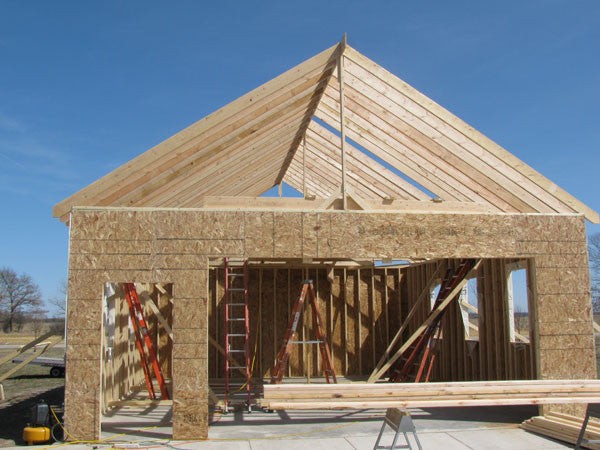
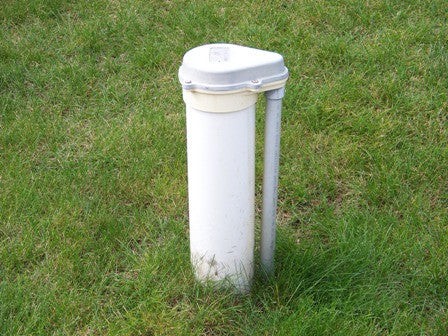
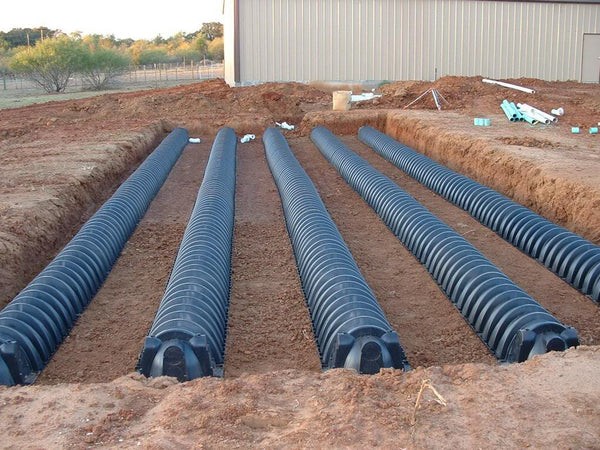
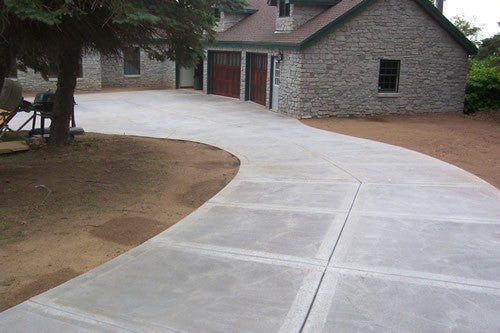
4. Why Modular Homes Are Often More Affordable
Modular homes often cost less than traditional stick-built homes due to efficiencies in the construction process.
4.1. Cost Savings Compared to Stick-Built Homes
Traditional on-site builders may charge $190 to $250/sq ft, and in some areas, this can exceed $325/sq ft for a simple ranch home. The same home built by traditional means could cost $283,000 to $373,000, representing significant savings with modular construction.
4.2. Factors Contributing to Lower Costs
- Factory Efficiency: Modular homes are built in a controlled factory environment, reducing waste and delays due to weather.
- Economies of Scale: Factories can purchase materials in bulk, leading to lower costs.
- Faster Construction: The modular construction process is often faster than traditional building, reducing labor costs.
5. Customization Options and Their Impact on Cost
Customizing your modular home allows you to create a living space that meets your specific needs and preferences. However, customization can also impact the overall cost.
5.1. Interior Customization
- Flooring: Upgrading from standard flooring to hardwood, tile, or other premium materials will increase the cost.
- Countertops: Granite, quartz, and other high-end countertops will add to the price.
- Cabinets: Custom cabinetry can significantly enhance the look and functionality of your kitchen and bathrooms, but it comes at a higher cost.
- Appliances: Selecting energy-efficient or high-end appliances will impact the overall cost.
- Fixtures: Upgrading lighting, plumbing, and other fixtures can add to the price.
5.2. Exterior Customization
- Siding: Choosing premium siding materials like brick, stone, or high-end vinyl will increase the cost.
- Roofing: Upgrading to a metal roof or other premium roofing material can add to the price.
- Windows and Doors: Energy-efficient windows and custom doors can improve the look and performance of your home, but they come at a higher cost.
- Landscaping: Adding landscaping features like patios, decks, and gardens will increase the overall project cost.
5.3. Structural Customization
- Floor Plan Changes: Modifying the floor plan to add or remove rooms, change room sizes, or alter the layout can impact the cost.
- Additional Stories: Adding a second story or finishing a basement will increase the overall square footage and cost.
- Specialty Rooms: Adding specialty rooms like a home theater, gym, or wine cellar will add to the price.
6. Financing Options for Modular Homes
Financing a modular home is similar to financing a traditional stick-built home. However, there are some unique considerations.
6.1. Types of Loans
- Construction Loans: These short-term loans cover the cost of building the modular home and preparing the site.
- Mortgages: Once the home is completed, you can refinance the construction loan into a traditional mortgage.
- FHA Loans: The Federal Housing Administration (FHA) offers loans for manufactured and modular homes.
- VA Loans: The Department of Veterans Affairs (VA) offers loans for eligible veterans to purchase modular homes.
- USDA Loans: The U.S. Department of Agriculture (USDA) offers loans for rural homebuyers, which can be used for modular homes.
6.2. Tips for Securing Financing
- Shop Around: Compare loan offers from multiple lenders to find the best terms and rates.
- Improve Your Credit Score: A higher credit score can help you qualify for better loan terms.
- Save for a Down Payment: A larger down payment can reduce your loan amount and monthly payments.
- Get Pre-Approved: Getting pre-approved for a loan can give you a better idea of your budget and make the home-buying process smoother.
7. Location Matters: Regional Cost Variations
The cost of building a modular home can vary significantly depending on your geographic location due to differences in labor costs, material prices, and local regulations.
7.1. Labor Costs
Labor costs can vary widely depending on the region. Areas with a higher cost of living typically have higher labor costs.
7.2. Material Prices
The cost of building materials like lumber, concrete, and roofing can also vary depending on the region. Areas with a higher demand for these materials may have higher prices.
7.3. Local Regulations
Local building codes and regulations can also impact the cost of building a modular home. Some areas may have stricter requirements than others, which can increase the cost.
8. Choosing the Right Modular Home Builder
Selecting the right builder is crucial for a successful modular home project.
8.1. Research and Due Diligence
- Check Credentials: Ensure the builder is licensed and insured.
- Read Reviews: Look for online reviews and testimonials from previous clients.
- Visit Model Homes: If possible, visit model homes built by the builder to assess the quality of their work.
- Get Multiple Bids: Obtain bids from multiple builders to compare prices and services.
8.2. Key Questions to Ask
- What is included in the base price?
- What customization options are available?
- What is the timeline for completion?
- What warranties are offered?
- Do you handle permits and inspections?
9. The Future of Modular Home Construction
Modular home construction is evolving, with advancements in technology and design leading to more affordable and sustainable housing options.
9.1. Technological Advancements
- 3D Printing: 3D printing technology is being used to create modular home components, reducing construction time and costs.
- Automation: Automation in factories is improving efficiency and reducing labor costs.
- Virtual Reality: Virtual reality is being used to design and visualize modular homes, allowing buyers to customize their homes before construction begins.
9.2. Sustainable Building Practices
- Green Materials: Modular home builders are increasingly using sustainable materials like recycled steel, bamboo, and reclaimed wood.
- Energy Efficiency: Modular homes are often designed to be highly energy-efficient, reducing utility costs and environmental impact.
- Waste Reduction: The modular construction process generates less waste than traditional building methods.
10. Consulting with Experts at HOW.EDU.VN
Navigating the complexities of modular home cost and construction can be challenging. Consulting with experts at HOW.EDU.VN can provide invaluable guidance and support.
10.1. Benefits of Expert Consultation
- Personalized Advice: Receive tailored advice based on your specific needs and budget.
- Cost-Saving Strategies: Learn strategies to reduce costs without sacrificing quality.
- Project Management: Get assistance with managing your modular home project from start to finish.
- Access to a Network of Professionals: Connect with experienced builders, lenders, and other professionals in the modular home industry.
10.2. How HOW.EDU.VN Can Help
At HOW.EDU.VN, we connect you with top-tier experts, including over 100 PhDs, who can provide in-depth consultations and customized solutions. Our services ensure you receive accurate, reliable, and actionable advice, saving you time and money.
FAQ: Frequently Asked Questions About Modular Home Costs
1. What is the average cost per square foot for a modular home?
The average cost per square foot for a modular home can range from $100 to $200, depending on the factors mentioned above.
2. Are modular homes cheaper than stick-built homes?
Yes, modular homes are often cheaper than stick-built homes due to efficiencies in the construction process.
3. What are the main factors that affect the cost of a modular home?
The main factors include size, customization, materials, location, contractor fees, and land development costs.
4. Can I customize a modular home?
Yes, modular homes can be customized to meet your specific needs and preferences.
5. What type of foundation is best for a modular home?
The best type of foundation for a modular home is typically a basement or crawlspace.
6. How do I finance a modular home?
You can finance a modular home with a construction loan, mortgage, FHA loan, VA loan, or USDA loan.
7. How long does it take to build a modular home?
The construction time for a modular home is typically shorter than for a stick-built home, often taking a few months.
8. Do modular homes appreciate in value?
Yes, modular homes can appreciate in value like traditional stick-built homes.
9. Are modular homes energy-efficient?
Yes, modular homes are often designed to be highly energy-efficient.
10. How do I find a reputable modular home builder?
You can find a reputable builder by checking credentials, reading reviews, visiting model homes, and getting multiple bids.
Ready to Build Your Dream Modular Home?
Building a modular home can be an affordable and efficient way to achieve your homeownership goals. By understanding the costs involved, exploring customization options, and consulting with experts, you can make informed decisions and create a home that meets your needs and budget.
Don’t navigate this complex process alone. Contact HOW.EDU.VN today to connect with our team of PhDs and expert consultants who can provide personalized guidance and support every step of the way. Let us help you turn your dream home into a reality.
Contact Us:
- Address: 456 Expertise Plaza, Consult City, CA 90210, United States
- WhatsApp: +1 (310) 555-1212
- Website: HOW.EDU.VN
Let HOW.EDU.VN guide you to success. Our team of over 100 PhDs is ready to assist you with expert advice tailored to your specific needs. Contact us today and experience the how.edu.vn difference.