Wondering how much concrete costs per yard? The cost of concrete per yard typically ranges from $150 to $180 or more, depending on location, mix design, and project specifics. At HOW.EDU.VN, we connect you with experienced professionals who can provide tailored advice and cost-effective solutions for your concrete projects.
Understanding the various factors influencing concrete pricing, such as material costs, labor rates, and transportation fees, will help you make informed decisions and achieve the best value for your investment. For expert guidance and personalized solutions, consult with our team of specialists at HOW.EDU.VN today and explore concrete project costs, ready mix concrete and material expenses.
1. Understanding Concrete Costs: An Overview
Concrete is a fundamental material in construction, used for everything from foundations to driveways. Determining the cost of concrete involves several key factors. Let’s break down the elements that affect the price you’ll pay per yard.
1.1. Factors Influencing Concrete Prices
Several factors influence the cost of concrete, making it essential to consider each aspect for accurate budgeting:
-
Material Costs: The price of raw materials like cement, aggregates (sand and gravel), and admixtures (chemicals added to the mix) significantly affects the overall cost.
-
Labor Rates: The cost of labor for mixing, pouring, and finishing concrete varies by location and the complexity of the job.
-
Transportation Fees: Delivery costs depend on the distance from the ready-mix plant to your job site and the volume of concrete needed.
-
Mix Design: The specific mix design required for your project (e.g., higher strength, special additives) can increase costs.
-
Location: Prices vary by region due to local market conditions, availability of materials, and demand.
1.2. National Average Concrete Prices in 2024
In the first half of 2024, the national average cost of ready-mix concrete was approximately $166.39 per cubic yard, according to the National Ready Mixed Concrete Association. However, prices typically range from $150 to $180 or more per cubic yard, depending on location and project requirements.
1.3. Historical Trends in Concrete Pricing
Examining historical data provides insight into how concrete prices have changed over time. Here’s a snapshot of national average prices per yard:
Year | Price per Yard |
---|---|
2023 | $160 |
2022 | $137 |
2020 | $125 |
2019 | $121 |
2018 | $113 |
2016 | $108 |
2014 | $98 |
2013 | $93 |
2008 | $75 |
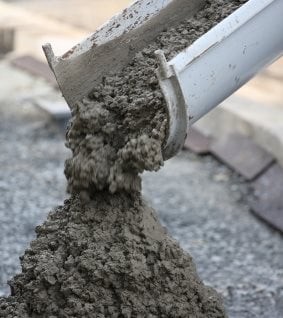
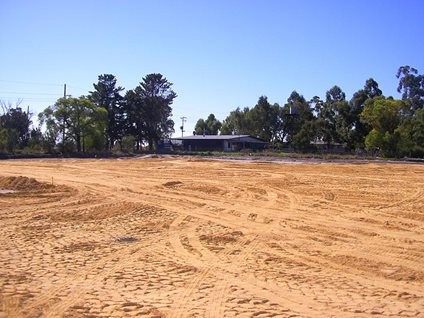
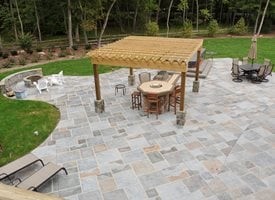
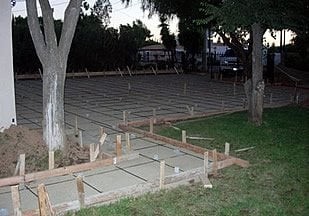
As the data indicates, concrete prices have generally increased over the years due to rising material, labor, and transportation costs.
2. Breaking Down the Cost: Materials, Labor, and More
Understanding the individual components of concrete pricing is crucial for effective budgeting. Let’s explore each element in detail.
2.1. Material Costs: Cement, Aggregates, and Admixtures
The primary materials in concrete include:
-
Cement: This is the binding agent that hardens and holds the mixture together. The type and quantity of cement affect the concrete’s strength and durability.
-
Aggregates: These include sand and gravel, which provide bulk and stability to the concrete mix. The quality and grading of aggregates influence the concrete’s workability and strength.
-
Admixtures: These are chemicals added to the mix to modify its properties, such as accelerating or retarding setting time, improving workability, or enhancing durability.
The costs of these materials can fluctuate based on market conditions, supply chain factors, and regional availability.
2.2. Labor Costs: Mixing, Pouring, and Finishing
Labor costs encompass the expenses associated with:
-
Mixing: Whether done on-site or at a ready-mix plant, mixing concrete requires skilled labor to ensure the proper proportions and consistency.
-
Pouring: This involves placing the concrete into forms and ensuring it is evenly distributed. Labor costs depend on the size and complexity of the pour.
-
Finishing: This includes leveling, smoothing, and texturing the concrete surface to achieve the desired appearance and functionality. Finishing labor costs vary based on the type of finish required (e.g., broom finish, smooth finish, decorative finish).
Labor rates differ by location, union status, and the contractor’s experience and reputation.
2.3. Transportation Costs: Delivery Fees and Distance
Transportation costs are influenced by:
-
Delivery Fees: Ready-mix suppliers charge delivery fees based on the distance from the plant to the job site and the volume of concrete being delivered.
-
Distance: Longer distances result in higher delivery costs due to fuel consumption, driver wages, and vehicle wear and tear.
-
Accessibility: Sites that are difficult to access may require additional equipment or labor, increasing transportation costs.
2.4. Additional Costs: Permits, Forms, and Reinforcement
Other potential costs to consider include:
-
Permits: Depending on the scope of your project, you may need to obtain permits from local authorities, which can add to your overall expenses.
-
Forms: These are temporary structures used to contain the concrete while it sets. The cost of forms depends on the size, shape, and complexity of the project.
-
Reinforcement: Steel reinforcement, such as rebar or wire mesh, is often used to increase the concrete’s strength and prevent cracking. The amount and type of reinforcement required will affect the cost.
3. Concrete Cost Per Square Foot: Estimating Slab Prices
While concrete is typically priced per cubic yard, contractors often provide estimates per square foot for slab projects. Let’s examine how to calculate and understand these costs.
3.1. Average Cost Per Square Foot for Plain Concrete Slabs
The average cost to pour a plain concrete slab ranges from $6.00 to $9.50 per square foot, including materials and labor. This price can vary based on the slab’s thickness, the complexity of the job, and local market conditions.
3.2. Calculating Concrete Slab Costs: A Step-by-Step Guide
To estimate the cost of a concrete slab:
-
Determine the Slab’s Dimensions: Measure the length and width of the area you want to cover with concrete.
-
Calculate the Square Footage: Multiply the length by the width to determine the total square footage.
-
Estimate the Cost: Multiply the square footage by the average cost per square foot ($6.00 to $9.50) to get an estimated total cost.
For example, a 200-square-foot slab might cost between $1,200 and $1,900, depending on the specific price per square foot.
3.3. Factors Affecting Square Foot Pricing
Several factors can influence the cost per square foot:
-
Slab Thickness: Thicker slabs require more concrete and reinforcement, increasing costs.
-
Site Preparation: Grading, excavation, and subbase preparation can add to the overall cost.
-
Complexity: Intricate designs or challenging site conditions can increase labor costs and the overall price per square foot.
4. Decorative Concrete Costs: Stamped, Stained, and More
Decorative concrete offers a high-end look without the high-end price tag of materials like natural stone or marble. Let’s explore the costs associated with different decorative options.
4.1. Types of Decorative Concrete and Their Costs
-
Stamped Concrete: This involves imprinting patterns into the concrete surface to mimic the look of brick, stone, or other materials. Stamped concrete typically costs $8 to $18 per square foot, depending on the complexity of the pattern.
-
Stained Concrete: This involves applying stains to the concrete surface to add color and depth. Stained concrete usually costs $2 to $8 per square foot, depending on the type of stain and the number of coats applied.
-
Polished Concrete: This involves grinding and polishing the concrete surface to create a smooth, glossy finish. Polished concrete typically costs $3 to $12 per square foot, depending on the level of polishing and any added dyes or aggregates.
4.2. Cost Factors for Decorative Concrete
Several factors can affect the cost of decorative concrete:
-
Design Complexity: Intricate patterns, multiple colors, and special details increase costs.
-
Surface Preparation: Existing concrete may require patching, grinding, or other preparation work, adding to the overall cost.
-
Sealers: Applying high-quality sealers protects the decorative finish and extends its lifespan, but also adds to the cost.
4.3. Comparing Decorative Concrete Costs to Other Materials
Decorative concrete is a mid-range option when compared to other materials. Outdoors, it is more affordable than natural stone and pavers but more expensive than asphalt and plain concrete. Indoors, it is more affordable than granite, marble, and hardwood but more expensive than laminates and ceramic tiles.
5. Estimating Concrete Costs for Outdoor Projects
Outdoor concrete projects, such as patios, driveways, and walkways, require careful planning and budgeting. Let’s explore the costs associated with these projects.
5.1. Patio Costs: Plain vs. Decorative
-
Plain Concrete Patio: A plain concrete patio typically costs $6 to $9.50 per square foot.
-
Decorative Concrete Patio: A decorative concrete patio, such as stamped or stained concrete, can range from $8 to $18 per square foot, depending on the design and finish.
The cost of a patio depends on its size, the complexity of the design, and any additional features, such as built-in seating or fire pits.
5.2. Driveway Costs: Factors to Consider
Driveway costs depend on several factors:
-
Size: Larger driveways require more concrete and labor, increasing costs.
-
Thickness: Driveways need to be thicker than patios to withstand vehicle traffic, adding to the material costs.
-
Reinforcement: Proper reinforcement is essential to prevent cracking and ensure the driveway’s longevity.
A typical concrete driveway costs between $6 and $12 per square foot, depending on these factors.
5.3. Walkway Costs: Design and Material Options
Walkway costs vary based on the design and materials used:
-
Plain Concrete Walkway: A plain concrete walkway typically costs $5 to $10 per square foot.
-
Decorative Concrete Walkway: A decorative concrete walkway can range from $7 to $15 per square foot, depending on the design and finish.
Additional features, such as borders, curves, and special finishes, can increase the cost of a walkway.
6. Estimating Concrete Costs for Indoor Projects
Indoor concrete projects, such as flooring and countertops, can add a modern and durable touch to your home. Let’s explore the costs associated with these projects.
6.1. Flooring Costs: Polished vs. Stained
-
Polished Concrete Flooring: Polished concrete flooring typically costs $3 to $12 per square foot, depending on the level of polishing and any added dyes or aggregates.
-
Stained Concrete Flooring: Stained concrete flooring usually costs $2 to $8 per square foot, depending on the type of stain and the number of coats applied.
The cost of concrete flooring depends on the size of the area, the existing condition of the slab, and any special finishes or designs.
6.2. Countertop Costs: Custom Designs and Finishes
Concrete countertops offer a unique and customizable option for kitchens and bathrooms. The cost of concrete countertops depends on several factors:
-
Size and Shape: Larger and more complex countertops require more material and labor, increasing costs.
-
Custom Designs: Special features, such as integrated sinks, drain boards, and decorative inlays, add to the cost.
-
Finishes: Polishing, staining, and sealing are essential for protecting and enhancing the countertop’s appearance.
A typical concrete countertop costs between $75 and $200 per square foot, depending on these factors.
6.3. Interior Wall Costs: Textures and Finishes
Concrete can also be used for interior walls, adding a modern and industrial aesthetic. The cost of concrete walls depends on:
-
Size: Larger walls require more material and labor, increasing costs.
-
Textures: Applying different textures, such as smooth, rough, or patterned finishes, affects the cost.
-
Finishes: Sealing and staining can enhance the wall’s appearance and protect it from moisture and stains.
Concrete walls typically cost between $8 and $25 per square foot, depending on these factors.
7. Finding the Best Concrete Contractors
Choosing the right contractor is crucial for ensuring the success of your concrete project. Here’s how to find the best professionals for the job.
7.1. Researching Local Contractors: Online Reviews and Referrals
Start by researching local concrete contractors online. Look for contractors with positive reviews, high ratings, and a proven track record of quality work. Ask friends, family, and neighbors for referrals to reputable contractors in your area.
7.2. Checking Credentials and Insurance
Before hiring a contractor, verify their credentials and insurance. Make sure they are licensed and insured to protect yourself from liability in case of accidents or damages.
7.3. Obtaining Multiple Quotes: Comparing Prices and Services
Get quotes from multiple contractors to compare prices and services. Make sure each quote includes a detailed breakdown of the costs, including materials, labor, and any additional fees.
7.4. Reviewing Portfolios and Past Projects
Ask contractors to provide portfolios of their past projects. Review their work to ensure they have experience with the type of concrete project you are planning. Visit completed projects, if possible, to assess the quality of their workmanship.
7.5. Communicating Your Expectations Clearly
Clearly communicate your expectations to the contractor. Discuss the scope of the project, the desired design and finish, and any specific requirements you may have. A clear understanding between you and the contractor will help ensure a successful outcome.
8. Tips for Saving Money on Concrete Projects
While concrete projects can be costly, there are several ways to save money without sacrificing quality.
8.1. Planning Ahead: Avoiding Rush Orders and Delays
Planning ahead can help you avoid rush orders and delays, which can increase costs. Schedule your project in advance and allow plenty of time for preparation, pouring, and curing.
8.2. Opting for Plain Concrete: Simple Designs and Finishes
Choosing plain concrete over decorative options can save money on materials and labor. Simple designs and finishes are typically less expensive than intricate patterns and special textures.
8.3. Preparing the Site Yourself: Grading and Excavation
Preparing the site yourself, such as grading and excavation, can reduce labor costs. However, make sure you have the necessary skills and equipment to do the job safely and effectively.
8.4. Purchasing Materials in Bulk: Discounts and Savings
Purchasing materials in bulk, such as cement and aggregates, can result in discounts and savings. Coordinate with your contractor to determine the quantities needed and take advantage of any available discounts.
8.5. Negotiating Prices: Getting the Best Deal
Negotiate prices with contractors and suppliers to get the best deal. Don’t be afraid to ask for discounts or compare prices from different sources.
9. Common Mistakes to Avoid
Avoiding common mistakes can save you time, money, and frustration on your concrete project.
9.1. Underestimating the Amount of Concrete Needed
Underestimating the amount of concrete needed can result in delays and additional costs. Use a concrete calculator to accurately estimate the quantity required for your project.
9.2. Neglecting Site Preparation: Proper Grading and Compaction
Neglecting site preparation can compromise the structural integrity of your concrete project. Ensure proper grading and compaction to provide a stable base for the concrete.
9.3. Using the Wrong Mix Design: Strength and Durability
Using the wrong mix design can affect the strength and durability of the concrete. Consult with a concrete specialist to determine the appropriate mix for your project.
9.4. Ignoring Weather Conditions: Pouring and Curing
Ignoring weather conditions can impact the quality of the concrete. Avoid pouring concrete in extreme temperatures or during heavy rain. Ensure proper curing to prevent cracking and ensure maximum strength.
9.5. Failing to Seal the Concrete: Protection and Longevity
Failing to seal the concrete can leave it vulnerable to stains, moisture, and damage. Apply a high-quality sealer to protect the concrete and extend its lifespan.
10. Future Trends in Concrete Pricing and Technology
The concrete industry is constantly evolving, with new technologies and trends emerging. Let’s explore some future developments.
10.1. Sustainable Concrete: Green Building Practices
Sustainable concrete is gaining popularity as builders and homeowners seek eco-friendly materials. This includes using recycled aggregates, reducing cement content, and incorporating supplementary cementitious materials.
10.2. Self-Healing Concrete: Innovations in Durability
Self-healing concrete contains additives that can repair cracks and extend the concrete’s lifespan. This technology reduces maintenance costs and improves the durability of concrete structures.
10.3. 3D-Printed Concrete: Automated Construction
3D-printed concrete is revolutionizing the construction industry, allowing for automated and efficient building processes. This technology can reduce labor costs and create complex designs with greater precision.
10.4. Smart Concrete: Sensors and Monitoring
Smart concrete incorporates sensors that monitor temperature, stress, and other parameters. This data can be used to optimize concrete performance and detect potential problems early on.
11. Concrete and Climate Change: Mitigating Environmental Impact
The production of concrete contributes to carbon emissions, making it essential to address its environmental impact.
11.1. Reducing Carbon Footprint: Alternative Materials
Using alternative materials, such as fly ash, slag, and silica fume, can reduce the carbon footprint of concrete. These materials are byproducts of other industrial processes and can replace a portion of the cement in the mix.
11.2. Carbon Capture Technologies: Reducing Emissions
Carbon capture technologies can reduce emissions from cement plants by capturing and storing carbon dioxide. This technology is still in development but has the potential to significantly reduce the environmental impact of concrete production.
11.3. Life Cycle Assessments: Evaluating Environmental Impact
Life cycle assessments evaluate the environmental impact of concrete from production to disposal. This analysis can help identify opportunities to reduce emissions and improve the sustainability of concrete projects.
12. Consulting with Experts at HOW.EDU.VN
Navigating the complexities of concrete costs and projects can be challenging. At HOW.EDU.VN, we connect you with experienced professionals who can provide tailored advice and cost-effective solutions.
12.1. Benefits of Consulting Experts
- Expert Advice: Get guidance from industry experts who understand the intricacies of concrete pricing and project management.
- Cost-Effective Solutions: Identify cost-saving opportunities without sacrificing quality or durability.
- Personalized Recommendations: Receive tailored recommendations based on your specific project requirements and budget.
- Risk Mitigation: Avoid common mistakes and potential pitfalls with expert guidance.
- Peace of Mind: Ensure the success of your concrete project with professional support.
12.2. How HOW.EDU.VN Can Help
At HOW.EDU.VN, we connect you with a network of experienced professionals who can provide expert advice and support for your concrete projects. Our team includes:
- Licensed Contractors: Experienced contractors who can handle all aspects of your concrete project, from site preparation to finishing.
- Concrete Specialists: Experts in mix design, material selection, and sustainable concrete practices.
- Project Managers: Professionals who can oversee your project from start to finish, ensuring it is completed on time and within budget.
12.3. Contact Us Today
Don’t navigate the complexities of concrete projects alone. Contact HOW.EDU.VN today to connect with experienced professionals who can help you achieve your goals. Our team is ready to provide expert advice, cost-effective solutions, and personalized support for your concrete project. Reach out to us at 456 Expertise Plaza, Consult City, CA 90210, United States. Whatsapp: +1 (310) 555-1212. Visit our website at HOW.EDU.VN for more information.
13. FAQ: Frequently Asked Questions About Concrete Costs
Here are some frequently asked questions about concrete costs to help you make informed decisions.
13.1. What is the average cost of concrete per yard?
The average cost of concrete per yard ranges from $150 to $180 or more, depending on location, mix design, and project specifics.
13.2. How is concrete pricing determined?
Concrete pricing is determined by several factors, including material costs, labor rates, transportation fees, mix design, and location.
13.3. What are the main components of concrete cost?
The main components of concrete cost include materials (cement, aggregates, admixtures), labor (mixing, pouring, finishing), transportation, permits, forms, and reinforcement.
13.4. How can I estimate the cost of a concrete slab?
To estimate the cost of a concrete slab, determine the slab’s dimensions, calculate the square footage, and multiply by the average cost per square foot ($6.00 to $9.50).
13.5. What is the difference between plain and decorative concrete costs?
Plain concrete typically costs $6 to $9.50 per square foot, while decorative concrete can range from $8 to $18 per square foot, depending on the design and finish.
13.6. How can I save money on concrete projects?
You can save money by planning ahead, opting for plain concrete, preparing the site yourself, purchasing materials in bulk, and negotiating prices.
13.7. What are some common mistakes to avoid in concrete projects?
Common mistakes include underestimating the amount of concrete needed, neglecting site preparation, using the wrong mix design, ignoring weather conditions, and failing to seal the concrete.
13.8. How can sustainable concrete practices reduce environmental impact?
Sustainable concrete practices, such as using recycled aggregates and reducing cement content, can reduce the carbon footprint of concrete.
13.9. How can HOW.EDU.VN help with my concrete project?
HOW.EDU.VN connects you with experienced professionals who can provide tailored advice, cost-effective solutions, and personalized support for your concrete project.
13.10. Where can I find expert advice on concrete projects?
You can find expert advice on concrete projects at HOW.EDU.VN, where we connect you with a network of experienced contractors, concrete specialists, and project managers.
14. Conclusion: Making Informed Decisions
Understanding the costs associated with concrete projects is essential for effective budgeting and planning. By considering the various factors that influence concrete pricing and seeking expert advice, you can make informed decisions and achieve the best value for your investment.
At HOW.EDU.VN, we are committed to providing you with the resources and support you need to succeed in your concrete projects. Contact us today to connect with experienced professionals who can help you navigate the complexities of concrete costs and achieve your goals.
Ready to get started on your concrete project? Contact how.edu.vn today for expert advice and personalized solutions.