The cost of concrete per yard typically ranges from $150 to $180 nationwide, but can fluctuate based on various factors; for a precise understanding and customized solutions, “HOW.EDU.VN” provides expert guidance. The price generally includes the concrete mix itself, with additional fees for delivery and labor, particularly impacting final concrete project costs. For homeowners aiming to undertake concrete projects, it’s essential to consider concrete prices, which vary significantly based on location and project specifications.
Table of Contents
- What Determines the Price of Concrete per Yard?
- Concrete Cost Breakdown: A Detailed Analysis
- Regional Price Variations: How Location Impacts Concrete Costs
- DIY vs. Professional Installation: Cost and Quality Considerations
- Decorative Concrete Options: Enhancing Value and Aesthetics
- Cost-Saving Tips for Your Concrete Project
- Future Trends in Concrete Pricing: What to Expect
- How to Calculate the Exact Amount of Concrete Needed for Your Project?
- Expert Advice from HOW.EDU.VN: Ensuring Project Success
- Frequently Asked Questions About Concrete Costs
1. What Determines the Price of Concrete per Yard?
The price of concrete per yard is not a static figure; it’s influenced by a multitude of factors that can cause considerable variation. Understanding these determinants is crucial for anyone planning a construction or home improvement project involving concrete. Let’s delve into the primary factors that dictate how much you’ll pay for concrete per yard.
1.1. Raw Materials Costs
The fundamental building blocks of concrete are cement, aggregates (such as sand and gravel), and water. The cost of these raw materials directly impacts the final price of concrete.
- Cement: Cement is the binder that holds the concrete mix together. Its price can fluctuate due to energy costs (as cement production is energy-intensive), environmental regulations, and supply-demand dynamics.
- Aggregates: These make up the bulk of the concrete mix and are sourced from quarries and sandpits. Transportation costs, environmental levies, and local availability influence their price.
- Water: While water is a relatively inexpensive component, its quality is crucial. In some regions, treated or specific-quality water may be required, adding to the cost.
1.2. Labor Costs
Labor is a significant component of concrete pricing, encompassing the wages of workers involved in mixing, delivering, pouring, and finishing the concrete.
- Mixing and Batching: Skilled operators are needed to ensure the concrete mix is consistent and meets project specifications.
- Delivery: Truck drivers and dispatchers are required to transport the concrete from the ready-mix plant to the job site efficiently.
- Pouring and Finishing: Experienced concrete finishers are essential for achieving a smooth, level surface. Their expertise is particularly valuable for decorative concrete projects.
1.3. Transportation Costs
Concrete is a perishable commodity; it must be transported and poured within a limited timeframe before it begins to set. Transportation costs depend on several variables.
- Distance: The farther the delivery distance from the concrete plant to the job site, the higher the transportation costs.
- Fuel Prices: Fluctuations in fuel prices directly affect transportation expenses.
- Trucking Fees: These cover the cost of operating and maintaining the concrete mixer trucks.
- Accessibility: Difficult-to-access sites may require specialized equipment or additional labor, increasing costs.
1.4. Location
Geographical location plays a pivotal role in concrete pricing due to variations in material availability, labor rates, and regional demand.
- Urban vs. Rural: Concrete prices tend to be higher in urban areas due to increased demand, higher labor costs, and stricter environmental regulations.
- Regional Demand: Areas experiencing construction booms or infrastructure development may see higher concrete prices due to increased demand.
- Local Regulations: Environmental regulations, permitting fees, and local taxes can influence the overall cost of concrete.
1.5. Mix Design and Additives
The specific mix design and any additives used can significantly affect the price of concrete.
- Mix Proportions: The ratio of cement, aggregates, and water in the mix determines its strength, durability, and workability. Specialty mixes may require higher cement content or specific aggregate types, increasing costs.
- Additives: Various additives can enhance concrete performance, such as air-entraining agents for freeze-thaw resistance, plasticizers for improved workability, and accelerators for faster setting times. These additives come at an additional cost.
1.6. Volume of Concrete Ordered
The volume of concrete ordered can impact the price per yard.
- Discounts: Ready-mix suppliers may offer volume discounts for larger orders.
- Minimum Order Fees: Small orders may incur additional fees to cover the cost of setup and delivery.
- Partial Load Charges: If you order less than a full truckload, you may be charged a partial load fee.
1.7. Time of Year
Concrete prices can fluctuate seasonally due to weather conditions and construction activity.
- Peak Season: During the peak construction season (typically spring and summer), demand for concrete increases, leading to higher prices.
- Off-Season: In colder climates, winter weather can hinder concrete pouring, reducing demand and potentially lowering prices. However, additional measures for cold-weather concreting may offset any cost savings.
1.8. Market Conditions
Overall economic conditions and market dynamics can influence concrete prices.
- Economic Growth: Strong economic growth and increased construction activity tend to drive up concrete prices.
- Supply Chain Disruptions: Disruptions in the supply chain, such as material shortages or transportation bottlenecks, can lead to price increases.
- Competition: The level of competition among ready-mix suppliers in your area can affect pricing.
1.9. Project Complexity
The complexity of your concrete project can impact costs beyond the price of the concrete itself.
- Site Preparation: Extensive site preparation, such as excavation, grading, and formwork, can add to the overall project cost.
- Reinforcement: The use of reinforcing steel (rebar or wire mesh) increases material and labor expenses.
- Finishing Requirements: Special finishing techniques, such as stamping, staining, or polishing, require skilled labor and specialized equipment, adding to the project cost.
By understanding these factors, you can better estimate the cost of concrete for your project and make informed decisions to manage expenses effectively. Remember to obtain quotes from multiple suppliers and contractors to compare prices and services. For expert guidance tailored to your specific needs, consult with the professionals at HOW.EDU.VN.
2. Concrete Cost Breakdown: A Detailed Analysis
Understanding the components that make up the total cost of a concrete project is essential for accurate budgeting and informed decision-making. Beyond the price per yard of the concrete mix itself, several additional expenses contribute to the overall cost. This section breaks down these costs in detail.
2.1. Materials
The cost of materials is a primary component, encompassing not only the concrete mix but also other essential items needed for the project.
- Concrete Mix: As previously discussed, the price per yard of concrete varies based on factors such as raw materials, mix design, and location.
- Formwork: Formwork is used to contain the concrete while it cures and takes shape. Materials include wood, aluminum, or steel. The cost depends on the size and complexity of the forms.
- Reinforcement: Reinforcing steel (rebar or wire mesh) adds strength and durability to the concrete. The amount needed depends on the project’s structural requirements.
- Additives and Sealers: Additives enhance concrete performance, while sealers protect the surface from damage. These materials add to the overall cost.
- Subbase Materials: Materials like gravel or sand are used to create a stable subbase beneath the concrete slab. The quantity and type of material depend on soil conditions and project specifications.
2.2. Labor
Labor costs include the wages paid to workers for various tasks, from site preparation to concrete finishing.
- Site Preparation: This involves clearing the area, excavation, grading, and compacting the soil.
- Formwork Installation: Skilled carpenters or formwork specialists are needed to construct and install the forms accurately.
- Concrete Pouring: Labor is required to place the concrete, spread it evenly, and consolidate it to remove air pockets.
- Finishing: Concrete finishers use specialized tools to create a smooth, level surface. Decorative finishes require additional skill and time.
- Curing: Proper curing is essential for concrete strength and durability. Labor is needed to apply curing compounds or keep the concrete moist.
2.3. Equipment
Various types of equipment are necessary for a concrete project, and the costs associated with their use must be factored in.
- Concrete Mixer: For smaller projects, a portable concrete mixer may be used.
- Wheelbarrows or Concrete Buggies: These are used to transport concrete from the mixer or truck to the pouring location.
- Vibrators: Vibrators consolidate the concrete and remove air pockets, improving its strength and density.
- Screeds and Floats: These tools are used to level and smooth the concrete surface.
- Power Trowels: Power trowels are used for finishing large concrete slabs, creating a smooth, professional look.
- Pumps: Concrete pumps are used to move concrete to hard-to-reach areas.
- Heavy Machinery: Excavators, graders, and loaders may be needed for site preparation.
2.4. Delivery
Delivery charges can significantly impact the total cost of a concrete project, especially for smaller orders.
- Ready-Mix Delivery Fees: Ready-mix suppliers typically charge a delivery fee based on the distance from the plant to the job site.
- Minimum Load Charges: If you order less than a full truckload, you may be charged a minimum load fee.
- Partial Load Charges: Similar to minimum load charges, partial load fees apply when you order less than a full truckload.
- Additional Trip Charges: If the concrete truck needs to make multiple trips to the job site, you may incur additional charges.
2.5. Site Access and Preparation
The ease of access to the job site and the amount of preparation required can affect costs.
- Accessibility: Difficult-to-access sites may require specialized equipment or additional labor, increasing costs.
- Obstructions: Obstacles such as trees, utility lines, or existing structures may need to be removed or worked around, adding to the project cost.
- Soil Conditions: Unstable or poorly drained soil may require additional preparation, such as soil stabilization or drainage improvements.
- Permits and Inspections: Depending on local regulations, you may need to obtain permits and inspections, which involve fees and potential delays.
2.6. Waste Disposal
Proper disposal of waste materials is essential for environmental compliance and can add to the project cost.
- Concrete Waste: Excess concrete must be disposed of properly, which may involve hauling it to a recycling facility or landfill.
- Formwork Waste: Used formwork materials must also be disposed of responsibly.
- Other Waste: Other waste materials, such as packaging and scrap materials, must be disposed of appropriately.
2.7. Contingency
It’s always wise to include a contingency in your budget to cover unexpected expenses.
- Unexpected Issues: Unforeseen problems, such as hidden underground utilities or changes in soil conditions, can arise during the project.
- Change Orders: Changes to the project scope or design may result in additional costs.
- Weather Delays: Inclement weather can delay the project, leading to increased labor and equipment costs.
By considering these various cost components, you can develop a comprehensive budget for your concrete project and avoid surprises along the way. Remember to obtain detailed quotes from multiple contractors and suppliers to compare prices and services. For expert advice and personalized solutions, contact the experienced professionals at HOW.EDU.VN.
3. Regional Price Variations: How Location Impacts Concrete Costs
The cost of concrete is significantly influenced by geographic location. Variations in local market conditions, transportation costs, material availability, and regulatory factors contribute to these regional price differences. Understanding these variations can help you budget more accurately for your concrete project.
3.1. Local Market Conditions
Local market conditions, including demand, competition, and economic factors, can significantly impact concrete prices.
- High-Demand Areas: Regions experiencing rapid growth or construction booms often see higher concrete prices due to increased demand.
- Competitive Markets: Areas with multiple concrete suppliers tend to have more competitive pricing.
- Economic Factors: Local economic conditions, such as employment rates and business activity, can influence demand and pricing.
3.2. Transportation Costs
Transportation costs are a major factor in concrete pricing, particularly for areas far from concrete plants or material sources.
- Distance to Plant: The farther the distance from the concrete plant to the job site, the higher the transportation costs.
- Fuel Prices: Fluctuations in fuel prices directly affect transportation expenses.
- Accessibility: Difficult-to-access sites may require specialized equipment or additional labor, increasing costs.
3.3. Material Availability
The availability of raw materials, such as cement and aggregates, can vary by region, affecting concrete prices.
- Local Sources: Regions with abundant local sources of cement and aggregates tend to have lower material costs.
- Import Costs: Areas that rely on imported materials may face higher prices due to transportation and import fees.
- Material Quality: The quality of available materials can also affect pricing.
3.4. Labor Costs
Labor rates vary significantly by region, influencing the overall cost of concrete projects.
- Union vs. Non-Union: Areas with strong union presence may have higher labor costs compared to non-union areas.
- Skilled Labor: Demand for skilled concrete finishers and other specialized workers can drive up labor rates.
- Cost of Living: Regions with higher costs of living generally have higher labor rates.
3.5. Regulatory Factors
Local regulations and environmental policies can impact concrete prices.
- Environmental Regulations: Stricter environmental regulations may increase the cost of concrete production and disposal.
- Permitting Fees: Permitting fees and inspection costs can vary by region, adding to the overall project cost.
- Local Taxes: Local taxes, such as sales tax, can affect the final price of concrete.
3.6. Climate and Seasonal Variations
Climate and seasonal variations can influence concrete prices, particularly in regions with harsh weather conditions.
- Cold Weather: In colder climates, winter weather can hinder concrete pouring, reducing demand and potentially lowering prices. However, additional measures for cold-weather concreting may offset any cost savings.
- Hot Weather: In hot climates, special precautions may be needed to prevent rapid drying and cracking, adding to the cost.
- Peak Season: During the peak construction season (typically spring and summer), demand for concrete increases, leading to higher prices.
3.7. Examples of Regional Price Variations
To illustrate the impact of regional factors on concrete prices, here are a few examples:
- Urban vs. Rural: Concrete prices tend to be higher in urban areas due to increased demand, higher labor costs, and stricter environmental regulations.
- Coastal vs. Inland: Coastal regions may face higher transportation costs for materials, while inland areas may have lower prices due to local material sources.
- Northeast vs. Southeast: The Northeast generally has higher labor costs and stricter regulations, leading to higher concrete prices compared to the Southeast.
By understanding the regional factors that influence concrete prices, you can better estimate the cost of your project and make informed decisions. Remember to obtain quotes from local suppliers and contractors to get the most accurate pricing for your area. For expert guidance tailored to your specific location and project needs, consult with the professionals at HOW.EDU.VN.
4. DIY vs. Professional Installation: Cost and Quality Considerations
When planning a concrete project, one of the first decisions you’ll face is whether to tackle it yourself (DIY) or hire a professional contractor. This choice involves weighing cost considerations against the desired quality and long-term durability of the finished product. Let’s explore the pros and cons of each approach.
4.1. DIY Concrete Projects
Opting for a DIY concrete project can be appealing, especially for homeowners looking to save money. However, it’s essential to understand the potential benefits and drawbacks.
4.1.1. Cost Savings
- Reduced Labor Costs: The most significant cost savings come from eliminating labor expenses. You won’t need to pay for a contractor’s hourly rates or fees.
- Material Sourcing: You may be able to source materials directly from suppliers, potentially negotiating better prices.
- Flexible Scheduling: DIY projects allow you to work at your own pace and schedule, avoiding potential delays caused by contractor availability.
4.1.2. Challenges and Considerations
- Skill and Experience: Concrete work requires specific skills and experience to ensure proper mixing, pouring, and finishing. Lack of expertise can lead to structural issues, surface imperfections, or premature failure.
- Time Commitment: DIY concrete projects can be time-consuming, especially for larger or more complex jobs.
- Equipment and Tools: You’ll need to acquire or rent the necessary equipment and tools, such as a concrete mixer, wheelbarrow, screed, floats, and finishing tools.
- Physical Demands: Concrete work is physically demanding, requiring lifting heavy materials, operating machinery, and working in various weather conditions.
- Warranty and Liability: DIY projects typically don’t come with a warranty, and you’re responsible for any issues or liabilities that may arise.
4.2. Professional Concrete Installation
Hiring a professional concrete contractor offers several advantages, but it also comes with higher costs.
4.2.1. Expertise and Quality
- Skilled Labor: Professional contractors have experienced crews who are trained in all aspects of concrete work, ensuring proper techniques and high-quality results.
- Proper Equipment: Contractors have access to specialized equipment and tools that can improve efficiency and accuracy.
- Mix Design Expertise: Professionals understand concrete mix designs and can tailor them to specific project requirements and local conditions.
- Compliance with Codes: Contractors are familiar with local building codes and regulations, ensuring that the project meets all necessary standards.
- Warranty and Insurance: Professional installations typically come with a warranty, protecting you against defects or premature failure. Contractors also carry insurance to cover potential liabilities.
4.2.2. Cost Considerations
- Labor Costs: Labor is a significant component of professional installation costs, including wages, benefits, and overhead.
- Project Management: Contractors handle project management tasks, such as scheduling, material procurement, and coordination, which adds to the overall cost.
- Permits and Fees: Contractors typically handle permit applications and inspections, which involve fees.
- Potential for Higher Material Costs: While contractors may have access to better pricing on materials, their markup can offset some of those savings.
4.3. Cost Comparison
To illustrate the cost differences between DIY and professional concrete installation, consider the following example:
Project: Pouring a 10×10 foot concrete patio
Item | DIY Cost | Professional Cost |
---|---|---|
Concrete (1.25 cubic yards) | $200 – $300 | $250 – $375 |
Formwork Materials | $50 – $100 | Included |
Reinforcement | $30 – $60 | Included |
Equipment Rental | $50 – $100 | Included |
Labor | $0 | $300 – $800 |
Permits | $0 – $50 | Included |
Total | $330 – $610 | $550 – $1525 |
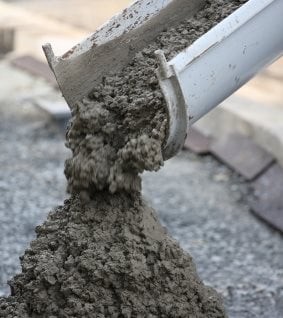

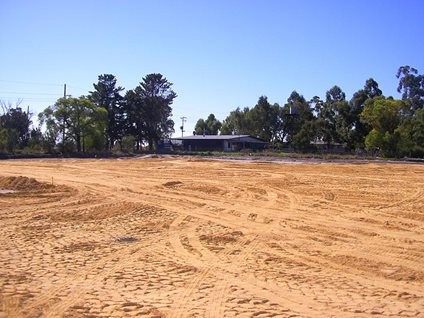
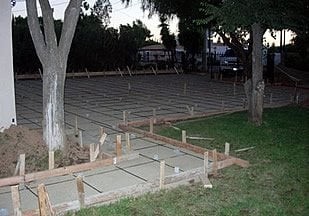
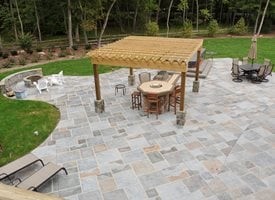
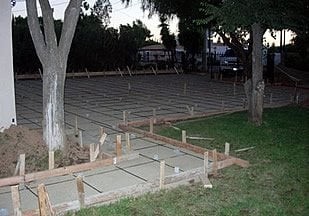
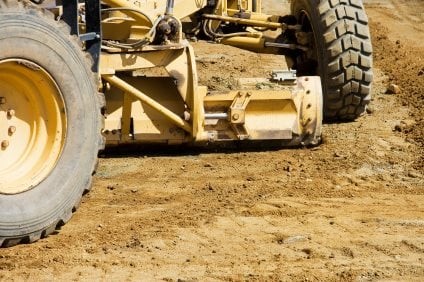
As you can see, DIY projects can save money on labor costs, but professional installations offer expertise, quality, and warranty protection.
4.4. Making the Right Choice
The decision to DIY or hire a professional depends on your skill level, time availability, budget, and desired outcome.
- DIY is suitable for:
- Small, simple projects with minimal structural requirements
- Homeowners with some concrete experience and skills
- Projects where cost savings are a primary concern
- Professional installation is recommended for:
- Large, complex projects with structural requirements
- Homeowners with limited concrete experience or skills
- Projects where quality, durability, and warranty are essential
Ultimately, the best approach depends on your individual circumstances and priorities. For expert advice and personalized recommendations, consult with the professionals at HOW.EDU.VN. We can help you assess your project needs and connect you with qualified concrete contractors in your area.
5. Decorative Concrete Options: Enhancing Value and Aesthetics
Decorative concrete is a versatile and cost-effective way to enhance the aesthetic appeal and value of your property. By using various techniques, such as stamping, staining, and polishing, you can transform plain concrete into a visually stunning surface that mimics the look of natural stone, brick, tile, or other high-end materials. Let’s explore the different decorative concrete options available.
5.1. Stamped Concrete
Stamped concrete involves pressing textured patterns into freshly poured concrete to create the look of various materials, such as:
- Natural Stone: Slate, flagstone, cobblestone, and other stone patterns can be replicated with remarkable realism.
- Brick: Stamped concrete can mimic the look of traditional brick pavers, creating a classic and timeless appearance.
- Tile: Tile patterns, such as those found in patios, walkways, and pool decks, can be replicated with stamped concrete.
- Wood: Stamped concrete can even mimic the look of wood planks, providing a durable and low-maintenance alternative to wood decking.
5.1.1. Cost Considerations
Stamped concrete typically costs more than plain concrete due to the additional labor and materials involved. However, it’s often more affordable than installing the actual materials it mimics. The cost varies depending on the complexity of the pattern, the number of colors used, and the size of the project.
5.1.2. Benefits of Stamped Concrete
- Aesthetics: Stamped concrete offers a wide range of design options, allowing you to create a unique and visually appealing surface.
- Durability: Stamped concrete is as durable as plain concrete, providing a long-lasting surface that can withstand heavy traffic and weather conditions.
- Low Maintenance: Stamped concrete is relatively low-maintenance, requiring only occasional cleaning and sealing to protect the surface.
- Increased Property Value: Decorative concrete can increase the value of your property by enhancing its curb appeal and aesthetic appeal.
5.2. Stained Concrete
Stained concrete involves applying a stain to the concrete surface to add color and depth. There are two main types of concrete stains:
- Acid-Based Stains: Acid-based stains react chemically with the concrete, creating a permanent color that won’t fade or peel. They produce a mottled, variegated look that resembles natural stone.
- Water-Based Stains: Water-based stains are more environmentally friendly and offer a wider range of color options. They penetrate the concrete surface but don’t react chemically, so they may be less durable than acid-based stains.
5.2.1. Cost Considerations
Stained concrete is generally more affordable than stamped concrete, but the cost varies depending on the type of stain used, the size of the project, and the complexity of the design.
5.2.2. Benefits of Stained Concrete
- Aesthetics: Stained concrete can add color and depth to plain concrete, creating a visually appealing surface.
- Durability: Stained concrete is durable and long-lasting, especially when sealed properly.
- Low Maintenance: Stained concrete is relatively low-maintenance, requiring only occasional cleaning and sealing.
- Versatility: Stained concrete can be used indoors or outdoors, on floors, walls, countertops, and other surfaces.
5.3. Polished Concrete
Polished concrete involves grinding and polishing the concrete surface to create a smooth, glossy finish. The process typically involves multiple grinding steps using progressively finer diamond-embedded abrasives.
5.3.1. Cost Considerations
Polished concrete can be more expensive than other decorative concrete options due to the specialized equipment and skilled labor required.
5.3.2. Benefits of Polished Concrete
- Aesthetics: Polished concrete offers a sleek, modern look that is popular in commercial and residential settings.
- Durability: Polished concrete is extremely durable and resistant to wear and tear.
- Low Maintenance: Polished concrete is easy to clean and maintain, requiring only occasional sweeping and mopping.
- Sustainability: Polished concrete is an environmentally friendly option because it utilizes the existing concrete slab, reducing the need for additional materials.
- Energy Efficiency: Polished concrete reflects light, reducing the need for artificial lighting and lowering energy costs.
5.4. Other Decorative Concrete Options
In addition to stamping, staining, and polishing, there are several other decorative concrete options available:
- Exposed Aggregate: This involves removing the top layer of cement paste to reveal the decorative aggregates beneath, such as pebbles, stones, or glass.
- Concrete Overlays: These are thin layers of polymer-modified concrete that are applied over existing concrete surfaces to create a new decorative finish.
- Concrete Countertops: Concrete countertops are a popular choice for kitchens and bathrooms, offering a durable and customizable surface.
- Vertical Concrete: Concrete can be used to create decorative walls, fireplaces, and other vertical surfaces.
By exploring the various decorative concrete options available, you can enhance the aesthetic appeal and value of your property. Remember to consult with a qualified concrete contractor to discuss your design ideas and budget. For expert advice and personalized recommendations, contact the professionals at HOW.EDU.VN. We can help you find the perfect decorative concrete solution for your project.
6. Cost-Saving Tips for Your Concrete Project
Managing costs effectively is crucial for any concrete project. By implementing some strategic cost-saving measures, you can minimize expenses without compromising the quality or durability of the finished product. Here are some practical tips to help you save money on your concrete project.
6.1. Plan Carefully
Thorough planning is essential for cost control.
- Accurate Measurements: Ensure accurate measurements of the project area to avoid ordering excess concrete.
- Detailed Design: Create a detailed design plan that specifies the dimensions, thickness, and finish of the concrete surface.
- Proper Site Preparation: Prepare the site properly to avoid costly delays or rework.
6.2. Obtain Multiple Quotes
Shopping around for the best prices is a simple way to save money.
- Contact Multiple Suppliers: Obtain quotes from multiple concrete suppliers to compare prices and delivery fees.
- Get Contractor Bids: Get bids from multiple concrete contractors to compare labor costs and services.
- Negotiate Prices: Don’t be afraid to negotiate prices with suppliers and contractors.
6.3. Choose the Right Mix Design
Selecting the appropriate mix design can optimize costs.
- Consider Project Requirements: Choose a mix design that meets the specific strength and durability requirements of your project.
- Avoid Over-Specifying: Avoid over-specifying the mix design, as higher-strength mixes can be more expensive.
- Use Local Materials: Use locally available materials to reduce transportation costs.
6.4. Optimize Concrete Thickness
Reducing the concrete thickness can save on material costs.
- Minimum Thickness: Use the minimum thickness required for the intended use of the concrete surface.
- Proper Subbase: Ensure a well-compacted subbase to provide adequate support and reduce the risk of cracking.
- Reinforcement: Use reinforcement (rebar or wire mesh) to increase the strength and durability of thinner concrete slabs.
6.5. Minimize Waste
Reducing waste can save on material and disposal costs.
- Accurate Ordering: Order the correct amount of concrete to avoid excess material.
- Proper Handling: Handle concrete carefully to minimize spills and waste.
- Recycle Concrete: If possible, recycle excess concrete or use it for other projects.
6.6. Consider DIY Options (with Caution)
DIY projects can save on labor costs, but proceed with caution.
- Assess Skill Level: Assess your skill level and experience before attempting a DIY concrete project.
- Start Small: Start with a small, simple project to gain experience.
- Seek Guidance: Seek guidance from experienced professionals or online resources.
6.7. Take Advantage of Seasonal Discounts
Concrete prices may fluctuate seasonally.
- Off-Season Projects: Consider scheduling your project during the off-season when demand is lower and prices may be more competitive.
- Winter Discounts: Some suppliers offer discounts on concrete during the winter months.
6.8. Reduce Transportation Costs
Minimizing transportation expenses can lead to savings.
- Local Suppliers: Choose a concrete supplier located close to your project site to reduce delivery fees.
- Full Loads: Order full truckloads of concrete to avoid partial load charges.
- Flexible Scheduling: Schedule your project during off-peak hours to avoid traffic delays and additional transportation costs.
6.9. Simplify Design
Simplifying the design can reduce labor and material costs.
- Straight Lines: Use straight lines and simple shapes to reduce formwork costs.
- Minimize Decorative Elements: Minimize the use of decorative elements, such as stamping or staining, to reduce labor and material costs.
- Standard Finishes: Choose standard finishes, such as broom finish, to reduce labor costs.
6.10. Proper Curing
Proper curing is essential for long-term durability.
- Prevent Cracking: Proper curing prevents cracking and increases the lifespan of the concrete surface, reducing the need for costly repairs or replacements.
- Curing Methods: Use appropriate curing methods, such as applying curing compounds or keeping the concrete moist.
By implementing these cost-saving tips, you can effectively manage expenses and ensure a successful concrete project without breaking the bank. Remember to consult with experienced professionals at HOW.EDU.VN for personalized advice and guidance.
7. Future Trends in Concrete Pricing: What to Expect
The concrete industry is constantly evolving, with new technologies, materials, and regulations shaping future pricing trends. Understanding these trends can help you anticipate future costs and make informed decisions about your concrete projects. Here are some key trends to watch for.
7.1. Rising Material Costs
Material costs are expected to continue rising in the coming years due to several factors.
- Increased Demand: Global demand for cement and aggregates is increasing, driven by infrastructure development and urbanization.
- Supply Chain Disruptions: Supply chain disruptions, such as material shortages and transportation bottlenecks, can lead to price increases.
- Environmental Regulations: Stricter environmental regulations may increase the cost of cement production and aggregate extraction.
7.2. Labor Shortages
The construction industry is facing a shortage of skilled labor, which is expected to drive up labor costs.
- Aging Workforce: The construction workforce is aging, and fewer young people are entering the industry.
- Training and Apprenticeships: There is a need for more training and apprenticeship programs to develop skilled workers.
- Immigration Policies: Changes in immigration policies can affect the availability of labor.
7.3. Sustainable Concrete
Sustainable concrete practices are gaining popularity, which may affect pricing.
- Recycled Materials: The use of recycled materials, such as recycled aggregates and supplementary cementitious materials (SCMs), can reduce the environmental impact of concrete and potentially lower costs.
- Carbon Sequestration: New technologies are being developed to capture and sequester carbon dioxide in concrete, which could increase costs initially but offer long-term environmental benefits.
- Green Building Standards: Green building standards, such as LEED, are encouraging the use of sustainable concrete practices.
7.4. Technology and Automation
Technology and automation are transforming the concrete industry, which could impact pricing.
- 3D Printing: 3D printing of concrete is becoming more common, which could reduce labor costs and construction time.
- Robotics: Robotics are being used for various tasks, such as concrete pouring and finishing, which could improve efficiency and reduce labor costs.
- Smart Concrete: Smart concrete technologies, such as sensors embedded in concrete, can monitor its condition and provide early warning of potential problems, which could reduce maintenance costs.
7.5. Regional Variations
Regional variations in concrete pricing are expected to persist.
- Demand and Supply: Areas with high demand and limited supply will likely continue to see higher prices.
- Local Regulations: Local regulations and environmental policies will continue to influence pricing.
- Transportation Costs: Transportation costs will remain a significant factor, particularly for areas far from material sources.
7.6. Government Infrastructure Spending
Government infrastructure spending can significantly impact concrete prices.
- Increased Demand: Increased government spending on infrastructure projects can drive up demand for concrete and other construction materials.
- Economic Growth: Infrastructure spending can stimulate economic growth, which can further increase demand for concrete.
7.7. Climate Change
Climate change is expected to have a growing impact on the concrete industry.
- Extreme Weather: Extreme weather events, such as floods and droughts, can disrupt concrete production and increase costs.
- Sea Level Rise: Sea level rise can damage concrete structures and increase the need for repairs and replacements.
- Resilient Concrete: There is a growing demand for resilient concrete that can withstand the effects of climate change.
By staying informed about these future trends, you can better anticipate changes in concrete pricing and make strategic decisions about your projects. Remember to consult with the experts at how.edu.vn for personalized advice and guidance.
8. How to Calculate the Exact Amount of Concrete Needed for Your Project?
Accurately calculating the amount of concrete needed for your project is crucial for cost control and minimizing waste. Underestimating can lead to delays and additional delivery fees, while overestimating results in unnecessary material costs and disposal expenses. Here’s a step-by-step guide to help you calculate the precise amount of concrete required.
8.1. Determine the Shape and Dimensions of the Project
The first step is to determine the shape and dimensions of the area you’ll be pouring concrete into. Common shapes include:
- Slabs (Rectangular or Square): Measure the length, width, and thickness of the slab.
- Circular Slabs: Measure the diameter and thickness of the slab.
- Walls: Measure the length, height, and thickness of the wall.
- Footings: Measure the length, width, and depth of the footing.
- Columns: