Planning a new patio, shed base, or other project requiring a solid foundation? How much does a 12×12 concrete slab cost is a crucial question, and HOW.EDU.VN provides the answers. Understanding the concrete slab cost, including material and labor, ensures your project stays on budget. Dive in to learn about slab thickness, concrete volume, and get expert tips for your concrete project, ensuring durable and cost-effective results. Explore expert advice on concrete slab pricing, factors influencing the price, and concrete construction considerations.
1. Understanding the Cost of a 12×12 Concrete Slab
Estimating the cost of a 12×12 concrete slab involves several factors, making it essential to understand the basics before diving into your project. From material prices to labor costs, knowing what to expect will help you budget effectively and avoid unexpected expenses. The average cost of a concrete slab is influenced by geographic location, the complexity of the job, and any special finishes you might desire. Let’s explore the primary aspects that affect the total cost.
1.1. Key Factors Influencing Concrete Slab Costs
Several elements influence the overall expense of your 12×12 concrete slab. These include:
- Thickness: A thicker slab requires more concrete, increasing material costs.
- Material Prices: The cost of concrete, including cement, sand, and aggregate, varies by location and supplier.
- Labor Costs: Hiring professionals to prepare the site, pour, and finish the slab adds to the overall expense.
- Site Preparation: Clearing vegetation, leveling the ground, and building forms are necessary steps that impact cost.
- Reinforcement: Adding rebar or wire mesh enhances the slab’s strength but increases material and labor costs.
- Finishes: Decorative finishes like stamping, staining, or sealing add to the expense.
- Permits: Local building permits may be required, adding an additional fee.
- Location: Costs vary by region due to differences in material availability, labor rates, and local regulations.
Understanding these factors will enable you to get a more accurate estimate for your project.
1.2. Average Cost Range for a 12×12 Concrete Slab
The average cost for a 12×12 concrete slab typically ranges from $576 to $1,728, but this can fluctuate based on the factors mentioned above. Here’s a breakdown by thickness:
Slab Thickness | Average Price for a 12×12 Slab |
---|---|
2 inches | $576 – $864 |
4 inches | $864 – $1,152 |
6 inches | $1,152 – $1,440 |
8 inches | $1,440 – $1,728 |
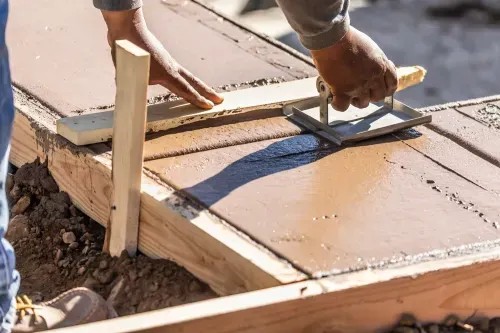
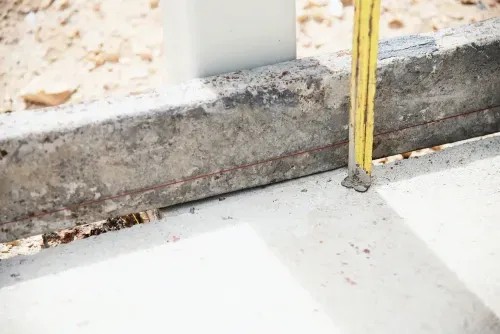
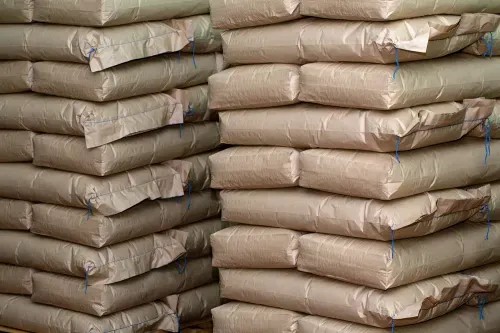
These prices are estimates and do not include labor, site preparation, or additional finishes.
1.3. Breaking Down the Costs: Materials, Labor, and Other Expenses
To understand the total cost, let’s break down the expenses involved in constructing a 12×12 concrete slab:
- Materials: This includes the cost of concrete mix, rebar or wire mesh (if used), formwork materials (lumber or forms), and any finishing products.
- Labor: Labor costs cover site preparation, formwork construction, concrete pouring, finishing, and cleanup.
- Site Preparation: This may include clearing the area, leveling the ground, compacting the soil, and adding a gravel base.
- Permits and Fees: Check with your local building department for permit requirements and associated fees.
- Finishes: If you opt for decorative finishes, factor in the cost of stamps, stains, sealers, and any additional labor required.
- Equipment Rental: Renting equipment like a concrete mixer, wheelbarrow, or power screed can add to the expenses.
1.4. Understanding Different Concrete Grades and Their Impact on Slab Cost
The grade of concrete used significantly influences the cost and performance of a 12×12 slab. Different grades offer varying levels of strength, durability, and suitability for specific applications. Opting for the right concrete grade is crucial for ensuring the longevity and stability of your slab.
Common Concrete Grades
- 2500 PSI: Suitable for light-duty applications such as walkways and patios. It’s less expensive but not ideal for heavy loads.
- 3000 PSI: A standard choice for residential slabs, driveways, and garage floors. Offers a good balance of strength and cost.
- 4000 PSI: Recommended for heavier loads and commercial applications. Provides increased durability and resistance to cracking.
- 5000 PSI and Higher: Used in specialized applications that require high strength and durability, such as structural foundations and industrial floors.
Impact on Slab Cost
Higher-grade concrete mixes generally cost more due to the increased cement content and specialized additives. While the initial investment is higher, the long-term benefits of enhanced durability and resistance to wear and tear can outweigh the added expense. Consulting with a concrete professional at HOW.EDU.VN can help you determine the most appropriate concrete grade for your specific needs and budget.
1.5. The Role of Concrete Reinforcement in Overall Cost
Reinforcing concrete slabs with materials like rebar or wire mesh can significantly increase their strength and durability. While reinforcement adds to the initial cost, it can also reduce the likelihood of cracking and structural failure, potentially saving money on repairs in the long run. Understanding the types of reinforcement available and their impact on overall cost is essential for making informed decisions.
Types of Concrete Reinforcement
- Rebar: Steel reinforcing bars are commonly used in thicker slabs to provide tensile strength and prevent cracking.
- Wire Mesh: Welded wire mesh is often used in thinner slabs to distribute loads and minimize cracking.
- Fiber Reinforcement: Synthetic or steel fibers can be added to the concrete mix to enhance its resistance to cracking and improve its overall durability.
Impact on Slab Cost
The cost of reinforcement depends on the type of material used, the spacing and size of the reinforcement, and the labor required for installation. Rebar typically costs more than wire mesh but provides greater strength. Fiber reinforcement can be a cost-effective alternative for certain applications. Working with a structural engineer or concrete contractor at HOW.EDU.VN can help you determine the optimal reinforcement strategy for your 12×12 slab, balancing cost and performance.
2. Detailed Cost Analysis Based on Slab Thickness
The thickness of your concrete slab is a primary determinant of its cost. Different thicknesses are suitable for various applications, and understanding these requirements is essential for budgeting correctly.
2.1. Cost of a 12×12 Concrete Slab 4 Inches Thick
A 4-inch thick slab is commonly used for patios, walkways, and shed bases. The average cost for materials alone ranges from $864 to $1,152. This does not include labor, site preparation, or additional finishes.
2.2. Cost of a 12×12 Concrete Slab 6 Inches Thick
A 6-inch thick slab is suitable for driveways and light vehicle parking areas. The material cost typically ranges from $1,152 to $1,440. Again, this excludes labor, site preparation, and finishing costs.
2.3. Comparison: 4-Inch vs. 6-Inch Slab – Which is Right for Your Project?
Choosing between a 4-inch and 6-inch slab depends on the intended use and load requirements. A 4-inch slab is adequate for light-duty applications, while a 6-inch slab is necessary for heavier loads. The following table provides a comparison:
Feature | 4-Inch Slab | 6-Inch Slab |
---|---|---|
Common Use | Patios, walkways, shed bases | Driveways, light vehicle parking areas |
Material Cost | $864 – $1,152 | $1,152 – $1,440 |
Load Capacity | Lower | Higher |
Durability | Moderate | High |
Site Preparation | Less extensive | More extensive |
Labor Costs | Lower | Higher |
Best For | Areas with minimal weight and foot traffic | Areas with vehicle traffic and heavier loads |
2.4. Calculating the Exact Volume of Concrete Needed
Accurately calculating the volume of concrete required is crucial for controlling costs and minimizing waste. Underestimating can lead to project delays and additional expenses, while overestimating results in unnecessary material costs.
Step-by-Step Calculation
- Determine Slab Dimensions: For a 12×12 slab, the length and width are both 12 feet.
- Choose Slab Thickness: Decide on the appropriate thickness (e.g., 4 inches or 6 inches) based on the intended use.
- Convert Thickness to Feet: Divide the thickness in inches by 12 to convert it to feet. For example, 4 inches is 0.33 feet, and 6 inches is 0.5 feet.
- Calculate Volume in Cubic Feet: Multiply the length, width, and thickness in feet:
- For a 4-inch slab: 12 ft x 12 ft x 0.33 ft = 47.52 cubic feet
- For a 6-inch slab: 12 ft x 12 ft x 0.5 ft = 72 cubic feet
- Convert Volume to Cubic Yards: Divide the volume in cubic feet by 27 (since 1 cubic yard = 27 cubic feet):
- For a 4-inch slab: 47.52 cubic feet / 27 = 1.76 cubic yards
- For a 6-inch slab: 72 cubic feet / 27 = 2.67 cubic yards
Importance of Accuracy
Accurate calculations not only help in ordering the correct amount of concrete but also ensure structural integrity and prevent future issues. Always double-check your measurements and consider adding a small buffer (5-10%) to account for spillage and uneven surfaces. Consulting with concrete professionals at HOW.EDU.VN can provide precise calculations tailored to your specific project needs.
2.5. The Impact of Site Preparation on the Final Cost
Proper site preparation is a critical step that significantly influences the overall cost and longevity of a concrete slab. Adequate preparation ensures a stable and level base, preventing issues like cracking, settling, and water damage. Failing to properly prepare the site can lead to costly repairs and premature slab failure.
Essential Site Preparation Steps
- Clearing and Grubbing: Remove all vegetation, topsoil, and organic matter from the site.
- Excavation and Grading: Excavate the area to the required depth and grade to ensure proper drainage.
- Compaction: Compact the soil using a plate compactor or roller to create a stable base.
- Base Material: Add a layer of gravel or crushed stone to improve drainage and load distribution.
- Formwork: Construct a sturdy form around the perimeter of the slab to contain the concrete during pouring.
Impact on Final Cost
The cost of site preparation depends on the condition of the existing ground, the amount of excavation required, and the type of base material used. More extensive site preparation, such as dealing with unstable soil or significant grading challenges, will increase the overall cost. However, investing in thorough site preparation is a worthwhile investment that can save money in the long run by preventing costly repairs. Experts at HOW.EDU.VN can assess your site and provide a detailed plan to ensure proper preparation.
3. Labor Costs: DIY vs. Hiring Professionals
Deciding whether to DIY or hire professionals for your concrete slab project is a significant consideration. Each option has its pros and cons regarding cost, time, and expertise.
3.1. Estimating Labor Costs for Professional Installation
Professional installation ensures the job is done correctly and efficiently. Labor costs can vary widely based on location, contractor experience, and the complexity of the project. On average, labor costs can range from $4 to $8 per square foot. For a 12×12 slab (144 square feet), this translates to $576 to $1,152.
3.2. DIY Concrete Slab: Potential Savings and Hidden Costs
Opting for a DIY approach can save on labor costs, but it also comes with potential hidden costs. While you avoid paying for professional labor, you’ll need to purchase or rent equipment, and you may encounter unexpected challenges that increase material costs.
3.3. Pros and Cons: DIY vs. Professional Installation
Feature | DIY | Professional Installation |
---|---|---|
Cost | Lower upfront, potential hidden costs | Higher upfront, fewer surprises |
Time | More time-consuming | Quicker |
Expertise | Requires knowledge and skill | Guaranteed quality and expertise |
Equipment | Rental or purchase required | Included in labor costs |
Risk | Higher risk of errors and rework | Lower risk of errors and rework |
Best For | Small projects, experienced DIYers | Large projects, those seeking quality assurance |
3.4. Selecting the Right Concrete Contractor
Choosing the right contractor is essential for ensuring the success of your concrete slab project. A qualified contractor brings expertise, experience, and the right equipment to deliver high-quality results. Taking the time to research and select the right professional can save you money and stress in the long run.
Key Considerations When Selecting a Contractor
- Check Credentials: Verify that the contractor is licensed, insured, and bonded in your local area.
- Review Experience: Look for a contractor with a proven track record of successful concrete slab installations.
- Ask for References: Contact previous clients to inquire about their experience with the contractor’s workmanship and professionalism.
- Obtain Multiple Quotes: Get detailed cost estimates from several contractors to compare pricing and services.
- Read Reviews: Check online reviews and testimonials to gauge the contractor’s reputation and customer satisfaction.
- Assess Communication: Choose a contractor who communicates clearly, responds promptly, and is willing to address your concerns.
The Value of Professional Expertise
A skilled concrete contractor not only ensures proper installation but also provides valuable insights into site preparation, concrete mix selection, and finishing techniques. Their expertise can help you avoid common pitfalls and achieve a durable, long-lasting concrete slab. HOW.EDU.VN offers resources and expert consultations to help you find and vet the best contractors for your project.
3.5. Navigating Permit Requirements and Regulations
Obtaining the necessary permits and complying with local building regulations is a crucial step in any concrete slab project. Failing to do so can result in fines, project delays, and even legal issues. Understanding the permit requirements in your area and ensuring compliance is essential for a smooth and successful project.
Understanding Local Requirements
- Contact Local Building Department: Reach out to your local building department to inquire about permit requirements for concrete slabs.
- Review Building Codes: Familiarize yourself with local building codes and regulations related to concrete construction.
- Submit Permit Application: Prepare and submit a detailed permit application, including site plans, construction drawings, and any required documentation.
- Schedule Inspections: Coordinate with the building department to schedule inspections at various stages of the project, such as after site preparation, formwork installation, and concrete pouring.
- Obtain Final Approval: Once the project is complete and all inspections have been passed, obtain final approval from the building department.
Ensuring Compliance
Compliance with permit requirements and building regulations not only ensures the safety and structural integrity of your concrete slab but also protects you from potential legal liabilities. HOW.EDU.VN offers resources and expert guidance to help you navigate the permit process and ensure that your project meets all applicable standards.
4. Optimizing Costs Without Compromising Quality
While staying within budget is crucial, compromising on quality can lead to costly repairs down the line. Here are some strategies to optimize costs without sacrificing the integrity of your concrete slab.
4.1. Choosing the Right Time of Year for Concrete Pouring
The time of year can affect concrete pouring. Ideal conditions are typically in the spring or fall when temperatures are moderate. Extreme heat or cold can affect the curing process, leading to cracks and other issues.
4.2. Selecting Cost-Effective Concrete Mixes
Different concrete mixes have varying prices. Standard mixes are suitable for most residential applications, while specialized mixes with additives can increase costs. Discuss your needs with a concrete supplier to find a cost-effective option.
4.3. Minimizing Waste: Accurate Measurement and Ordering
Accurate measurements and careful ordering can minimize waste. Over-ordering leads to unnecessary expenses, while under-ordering can cause delays and additional costs. Use online calculators and consult with professionals to ensure you order the correct amount.
4.4. Comparing Material Costs from Different Suppliers
Material costs can vary significantly between suppliers, so it’s essential to shop around and compare prices. Obtaining quotes from multiple suppliers allows you to find the best deals on concrete, reinforcement, and other materials. Don’t hesitate to negotiate prices or ask about discounts for bulk orders.
Strategies for Reducing Material Costs
- Get Multiple Quotes: Contact several suppliers and request detailed price quotes for all necessary materials.
- Compare Prices: Analyze the quotes to identify the most cost-effective options, considering both price and quality.
- Negotiate Prices: Don’t be afraid to negotiate prices with suppliers, especially if you’re placing a large order.
- Consider Alternatives: Explore alternative materials that may offer similar performance at a lower cost.
- Buy in Bulk: If possible, purchase materials in bulk to take advantage of volume discounts.
- Check for Sales: Keep an eye out for sales, promotions, and clearance events that can help you save money on materials.
The Importance of Quality
While it’s important to minimize material costs, never compromise on quality. Lower-quality materials may be cheaper upfront, but they can lead to premature failure and costly repairs in the long run. Experts at HOW.EDU.VN can help you strike the right balance between cost and quality.
4.5. Exploring Decorative Concrete Options on a Budget
Adding decorative finishes to your concrete slab can enhance its appearance and increase its value. However, decorative concrete can also be expensive. Fortunately, there are several ways to achieve a stylish look without breaking the bank.
Cost-Effective Decorative Concrete Options
- Staining: Concrete stains are an affordable way to add color and depth to your slab.
- Stamped Concrete: Stamped concrete can mimic the look of more expensive materials like brick or stone at a fraction of the cost.
- Exposed Aggregate: Exposing the aggregate in the concrete mix can create a unique and visually appealing surface.
- Polished Concrete: Polishing concrete can create a sleek, modern look that is both durable and cost-effective.
- Overlays: Concrete overlays can be applied to existing slabs to create a new decorative surface.
DIY vs. Professional Installation
Some decorative concrete options, such as staining and overlays, can be installed by homeowners with some DIY experience. However, more complex techniques like stamping and polishing are best left to professionals. Consulting with decorative concrete specialists at HOW.EDU.VN can help you choose the right option for your budget and skill level.
5. Long-Term Cost Considerations: Maintenance and Repairs
The initial cost of a concrete slab is just one aspect of the overall expense. Long-term maintenance and potential repairs should also be considered to ensure the slab remains in good condition for years to come.
5.1. Routine Maintenance to Extend Slab Lifespan
Regular maintenance can significantly extend the lifespan of your concrete slab and prevent costly repairs. This includes:
- Sealing: Applying a concrete sealer every 1-3 years protects the slab from water damage, stains, and deicing salts.
- Cleaning: Regularly cleaning the slab removes dirt, debris, and spills that can cause stains and deterioration.
- Crack Sealing: Promptly sealing any cracks that appear prevents water from penetrating and causing further damage.
- Joint Maintenance: Maintaining expansion joints ensures they function properly to accommodate movement and prevent cracking.
5.2. Common Concrete Slab Problems and Repair Costs
Despite proper maintenance, concrete slabs can develop problems over time. Common issues include:
- Cracking: Cracks can occur due to shrinkage, settling, or overloading. Repair costs range from $100 to $500, depending on the extent of the damage.
- Spalling: Spalling is the breaking away of the concrete surface. Repairing spalling can cost between $200 and $800.
- Settling: Settling occurs when the soil beneath the slab shifts. Repairing settling issues can range from $500 to $2,000 or more.
- Heaving: Heaving is the upward movement of the slab due to frost or expansive soils. Repairing heaving can cost between $500 and $3,000.
5.3. Budgeting for Potential Repairs: Setting Aside a Contingency Fund
It’s wise to set aside a contingency fund for potential repairs. Aim to allocate 5-10% of the initial project cost to cover unforeseen issues.
5.4. The Impact of Environmental Factors on Long-Term Costs
Environmental factors play a significant role in the long-term durability and maintenance costs of a concrete slab. Exposure to extreme temperatures, moisture, and chemical substances can accelerate deterioration and increase the likelihood of repairs. Understanding these environmental impacts and taking proactive measures can help minimize long-term costs.
Key Environmental Considerations
- Temperature Fluctuations: Repeated freezing and thawing cycles can cause concrete to crack and spall.
- Moisture Exposure: Excessive moisture can lead to efflorescence, mold growth, and corrosion of reinforcement.
- Chemical Exposure: Contact with deicing salts, fertilizers, and other chemicals can damage the concrete surface.
- UV Radiation: Prolonged exposure to sunlight can cause discoloration and degradation of the concrete.
- Soil Conditions: Expansive soils can exert pressure on the slab, leading to cracking and heaving.
Mitigating Environmental Impacts
- Sealing: Apply a high-quality concrete sealer to protect the slab from moisture and chemical damage.
- Drainage: Ensure proper drainage to prevent water from pooling around the slab.
- Proper Mix Design: Use a concrete mix that is appropriate for the local climate and soil conditions.
- Reinforcement: Reinforce the slab with rebar or wire mesh to increase its resistance to cracking.
- Regular Maintenance: Inspect the slab regularly and address any issues promptly to prevent further damage.
Seeking Expert Advice
Consulting with concrete professionals at HOW.EDU.VN can provide valuable insights into the environmental factors that may affect your concrete slab and help you develop a comprehensive maintenance plan to minimize long-term costs.
5.5. Maximizing the Resale Value of Your Property with a Well-Maintained Slab
A well-maintained concrete slab can enhance the resale value of your property by improving its curb appeal, functionality, and overall condition. Potential buyers are often impressed by features that are well-cared for and show attention to detail. Investing in regular maintenance and timely repairs can make your property more attractive and command a higher selling price.
Benefits of a Well-Maintained Slab
- Enhanced Curb Appeal: A clean, crack-free concrete slab can improve the overall appearance of your property.
- Increased Functionality: A well-maintained slab provides a safe and usable surface for outdoor activities.
- Improved Structural Integrity: A structurally sound slab demonstrates that the property has been well-cared for.
- Reduced Liability: A slab that is free of hazards like cracks and uneven surfaces can reduce the risk of accidents and injuries.
- Positive Impression: A well-maintained slab creates a positive impression on potential buyers, suggesting that the property is in good condition.
Marketing Your Well-Maintained Slab
When selling your property, be sure to highlight the features of your well-maintained concrete slab in your marketing materials. Emphasize its durability, functionality, and aesthetic appeal. Provide documentation of any maintenance or repairs that have been performed to demonstrate your commitment to preserving the property’s value. HOW.EDU.VN offers resources and expert advice to help you showcase the benefits of your concrete slab and maximize its impact on potential buyers.
6. Expert Advice and Resources from HOW.EDU.VN
Navigating the complexities of concrete slab construction can be challenging. HOW.EDU.VN offers a wealth of expert advice and resources to help you make informed decisions and ensure the success of your project.
6.1. Accessing Expert Consultations for Personalized Advice
HOW.EDU.VN connects you with experienced professionals who can provide personalized advice tailored to your specific needs. Whether you need help with site preparation, concrete mix selection, or decorative finishes, our experts are here to guide you.
6.2. Utilizing Online Calculators and Planning Tools
Our website features a range of online calculators and planning tools to simplify the process of estimating costs and planning your project. These tools can help you determine the amount of concrete needed, calculate rebar requirements, and estimate labor costs.
6.3. Reading Case Studies and Success Stories
Explore our collection of case studies and success stories to learn from others who have successfully completed concrete slab projects. These stories provide valuable insights and inspiration.
6.4. Staying Updated with the Latest Industry Trends and Innovations
The concrete industry is constantly evolving, with new materials, techniques, and technologies emerging all the time. Staying updated with the latest trends and innovations can help you make more informed decisions and achieve better results. HOW.EDU.VN provides a platform for continuous learning and professional development, keeping you at the forefront of the concrete industry.
Key Industry Trends
- Sustainable Concrete: Environmentally friendly concrete mixes that reduce carbon emissions and minimize waste.
- Self-Healing Concrete: Concrete that can automatically repair cracks and extend its lifespan.
- Smart Concrete: Concrete embedded with sensors that monitor its condition and provide real-time data.
- 3D-Printed Concrete: Concrete structures that are built using 3D printing technology.
- High-Performance Concrete: Concrete mixes that offer superior strength, durability, and resistance to environmental factors.
Benefits of Staying Informed
By staying informed about the latest industry trends and innovations, you can:
- Reduce Costs: Implement new technologies that can improve efficiency and lower material costs.
- Improve Quality: Use advanced materials and techniques to enhance the performance and durability of your concrete slab.
- Minimize Environmental Impact: Choose sustainable concrete options that reduce your carbon footprint.
- Stay Competitive: Keep up with the latest advancements to maintain a competitive edge in the market.
HOW.EDU.VN as a Resource
HOW.EDU.VN is committed to providing you with the latest information and resources to help you succeed in the concrete industry. Our team of experts regularly updates our website with articles, videos, and training materials covering the latest trends and innovations.
6.5. Connecting with a Community of Concrete Professionals
Building a network of fellow concrete professionals can provide invaluable support, insights, and opportunities for collaboration. Connecting with a community allows you to share experiences, ask questions, and learn from others in the field. HOW.EDU.VN fosters a vibrant community of concrete professionals, creating a platform for networking and knowledge sharing.
Benefits of Joining a Community
- Access to Expertise: Tap into the collective knowledge and experience of fellow professionals.
- Problem-Solving: Get help with challenging projects and troubleshoot common issues.
- Networking: Build relationships with potential partners, clients, and suppliers.
- Professional Development: Stay updated with the latest industry trends and best practices.
- Support and Encouragement: Find a supportive community that understands your challenges and celebrates your successes.
How to Connect with the HOW.EDU.VN Community
- Join Online Forums: Participate in online forums and discussion groups to connect with fellow professionals.
- Attend Industry Events: Attend conferences, trade shows, and workshops to network with industry leaders.
- Connect on Social Media: Follow HOW.EDU.VN and other concrete professionals on social media platforms like LinkedIn and Twitter.
- Share Your Expertise: Contribute your knowledge and insights to the community by writing articles, creating videos, or participating in webinars.
- Seek Mentorship: Find a mentor who can provide guidance and support as you navigate your career in the concrete industry.
7. Frequently Asked Questions (FAQs) About 12×12 Concrete Slabs
Here are some frequently asked questions to help you better understand the complexities of 12×12 concrete slabs.
7.1. How much does it cost to hire a professional to pour a 12×12 concrete slab?
Professional labor costs can range from $4 to $8 per square foot, so expect to pay between $576 and $1,152 for a 12×12 slab.
7.2. What is the best thickness for a 12×12 concrete slab?
The ideal thickness depends on the intended use. A 4-inch slab is suitable for patios and walkways, while a 6-inch slab is better for driveways.
7.3. Can I pour a concrete slab myself, or should I hire a professional?
DIY is possible for small projects, but professional installation ensures quality and minimizes risks.
7.4. What factors influence the cost of a concrete slab?
The cost of a concrete slab is affected by thickness, material prices, labor, site preparation, reinforcement, finishes, permits, and location.
7.5. How can I reduce the cost of my concrete slab project?
You can reduce costs by comparing material prices, selecting cost-effective concrete mixes, minimizing waste, and choosing the right time of year for pouring.
7.6. What are the maintenance requirements for a concrete slab?
Regular maintenance includes sealing, cleaning, crack sealing, and joint maintenance.
7.7. How do I calculate the amount of concrete needed for a 12×12 slab?
For a 4-inch slab: 12 ft x 12 ft x 0.33 ft = 47.52 cubic feet (1.76 cubic yards). For a 6-inch slab: 12 ft x 12 ft x 0.5 ft = 72 cubic feet (2.67 cubic yards).
7.8. What are the common problems with concrete slabs and how much do they cost to repair?
Common problems include cracking, spalling, and settling. Repair costs range from $100 to $2,000, depending on the extent of the damage.
7.9. Is it necessary to reinforce a 12×12 concrete slab?
Reinforcement with rebar or wire mesh can increase the slab’s strength and durability, especially for heavier loads.
7.10. How long will a concrete slab last?
With proper maintenance, a concrete slab can last for 20-30 years or more.
8. Conclusion: Making Informed Decisions for Your Concrete Slab Project
Estimating how much a 12×12 concrete slab costs involves understanding various factors, from material and labor expenses to maintenance and potential repairs. By carefully considering these aspects and seeking expert advice from HOW.EDU.VN, you can make informed decisions that ensure a successful and cost-effective project. Whether you opt for DIY or professional installation, proper planning and execution are key to achieving a durable and long-lasting concrete slab.
Ready to get started on your concrete slab project? Contact HOW.EDU.VN today for personalized advice and expert consultations. Our team of experienced professionals is here to help you navigate the complexities of concrete construction and ensure the success of your project. Don’t let the challenges of estimating costs and planning overwhelm you. Let us guide you towards achieving a durable, cost-effective, and visually appealing concrete slab that enhances the value and functionality of your property.
Contact us today at:
- Address: 456 Expertise Plaza, Consult City, CA 90210, United States
- WhatsApp: +1 (310) 555-1212
- Website: HOW.EDU.VN
Let how.edu.vn be your trusted partner in concrete construction, providing the expertise and resources you need to succeed.