How Much Is A Concrete Slab? Understanding the concrete slab cost is crucial for budgeting any construction or renovation project, and HOW.EDU.VN is here to provide expert insights. This guide breaks down all the factors influencing concrete slab costs, ensuring you’re well-informed and ready to make the best decisions for your project, including material pricing and thickness considerations.
1. Understanding Concrete Slab Costs: An In-Depth Analysis
Estimating the concrete slab installation cost accurately is essential for any construction project. Several key factors influence the final price. By understanding these variables, you can better prepare your budget and avoid unexpected expenses.
1.1. Key Factors Influencing Concrete Slab Costs
- Size and Thickness: The dimensions of the slab directly impact the amount of concrete needed, which significantly affects the overall cost. A larger and thicker slab requires more materials and labor.
- Concrete Mix: Different concrete mixes have different prices. For example, a standard mix for a patio will cost less than a high-strength mix required for a foundation.
- Site Preparation: The amount of site preparation needed can vary greatly. Clearing vegetation, leveling the ground, and compacting the soil all add to the cost.
- Reinforcement: The use of rebar or wire mesh to reinforce the slab can increase the cost, but it also enhances the slab’s durability and load-bearing capacity.
- Labor Costs: Labor rates vary by region and contractor. More complex projects may require specialized skills, which can also increase labor costs.
- Location: Prices for materials and labor vary significantly by geographic location. Urban areas tend to have higher costs than rural areas.
- Permits: Building permits are often required for concrete slab projects, and the cost of these permits can vary by municipality.
- Finishes: Decorative finishes such as stamped concrete or colored concrete can add to the cost but also enhance the aesthetic appeal of the slab.
1.2. Concrete Slab Cost Breakdown
To provide a clearer picture of the costs involved, here’s a typical breakdown:
Component | Percentage of Total Cost | Description |
---|---|---|
Materials | 40-60% | Includes the cost of concrete, reinforcement (rebar or wire mesh), gravel, sand, and any additives. |
Labor | 30-50% | Covers the cost of site preparation, formwork, pouring, finishing, and curing the concrete. |
Site Preparation | 5-10% | Includes clearing, leveling, and compacting the soil. May also involve removing existing structures or vegetation. |
Permits and Fees | 1-3% | Covers the cost of obtaining the necessary building permits and any inspection fees. |
Finishes and Extras | 5-15% | Includes the cost of any decorative finishes (stamping, coloring), sealants, and additional features like insulation or drainage systems. |
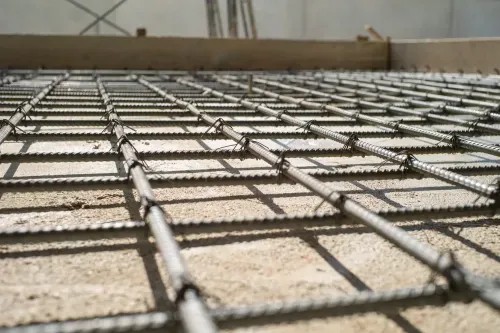
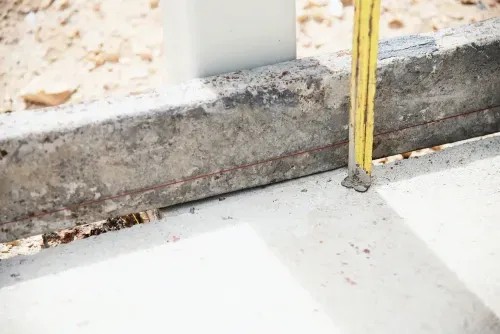
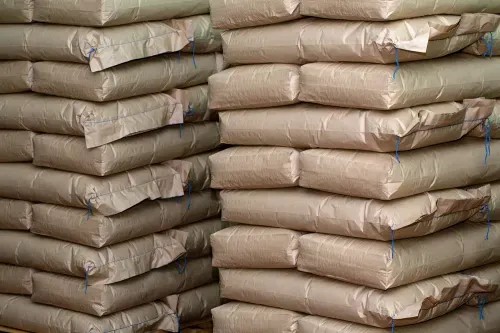
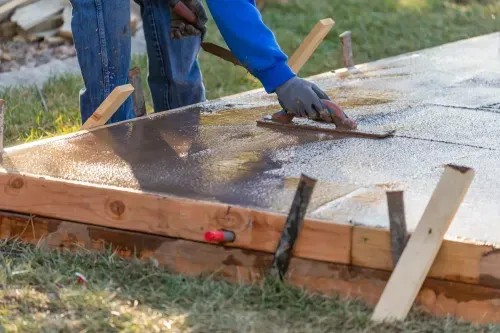
1.3. Getting an Accurate Estimate
To get the most accurate estimate for your concrete slab project, it’s recommended to:
- Obtain Multiple Quotes: Get quotes from at least three different contractors to compare prices and services.
- Provide Detailed Information: Provide contractors with as much detail as possible about your project, including the size, thickness, intended use, and any specific design requirements.
- Review the Contract Carefully: Before signing a contract, make sure you understand all the terms and conditions, including the scope of work, payment schedule, and warranty.
- Check References: Ask contractors for references and check them to ensure they have a good track record.
- Consider Long-Term Costs: While the initial cost is important, also consider the long-term maintenance and durability of the slab. Investing in higher-quality materials and workmanship can save you money in the long run.
2. Calculating Concrete Slab Costs for a 20×40 Slab
Calculating the cost of a 20×40 concrete slab involves several factors, including the thickness of the slab, the price of concrete, labor costs, and any additional materials needed. Let’s break down the process step-by-step.
2.1. Determining the Volume of Concrete Needed
The first step is to calculate the volume of concrete required for the slab. The volume depends on the dimensions of the slab and its thickness.
Formula:
Volume = Length x Width x Thickness
For a 20×40 slab, the length is 40 feet, and the width is 20 feet. The thickness can vary depending on the intended use of the slab. Common thicknesses are 4 inches and 6 inches.
-
For a 4-inch slab:
- Convert inches to feet: 4 inches = 4/12 feet = 0.333 feet
- Volume = 40 feet x 20 feet x 0.333 feet = 266.4 cubic feet
-
For a 6-inch slab:
- Convert inches to feet: 6 inches = 6/12 feet = 0.5 feet
- Volume = 40 feet x 20 feet x 0.5 feet = 400 cubic feet
Next, convert cubic feet to cubic yards, as concrete is typically sold by the cubic yard.
1 cubic yard = 27 cubic feet
-
For a 4-inch slab:
- Cubic yards = 266.4 cubic feet / 27 cubic feet/yard = 9.87 cubic yards
-
For a 6-inch slab:
- Cubic yards = 400 cubic feet / 27 cubic feet/yard = 14.81 cubic yards
2.2. Estimating the Cost of Concrete
The price of concrete varies depending on your location and the supplier. As of 2023, the average cost of concrete ranges from $120 to $180 per cubic yard. For this calculation, we’ll use an average price of $150 per cubic yard.
-
For a 4-inch slab:
- Cost of concrete = 9.87 cubic yards x $150/cubic yard = $1,480.50
-
For a 6-inch slab:
- Cost of concrete = 14.81 cubic yards x $150/cubic yard = $2,221.50
2.3. Factoring in Labor Costs
Labor costs can vary widely depending on the contractor and the complexity of the project. On average, labor costs range from $4 to $8 per square foot for pouring and finishing a concrete slab. For a 20×40 slab (800 square feet), the labor costs would be:
- Labor cost = 800 square feet x $6/square foot (average) = $4,800
2.4. Adding Costs for Site Preparation and Reinforcement
Additional costs to consider include site preparation and reinforcement.
-
Site Preparation: This can include clearing the area, leveling the ground, and compacting the soil. Site preparation costs can range from $0.50 to $1.50 per square foot. For a 20×40 slab:
- Site preparation cost = 800 square feet x $1/square foot (average) = $800
-
Reinforcement (Rebar): Rebar is often used to reinforce concrete slabs, especially for heavier applications. The cost of rebar can vary, but typically ranges from $0.30 to $0.60 per pound. For a 20×40 slab with rebar spaced 18 inches apart, you would need approximately 1210 feet of rebar, weighing around 300 pounds.
- Rebar cost = 300 pounds x $0.45/pound (average) = $135
2.5. Calculating Total Costs
Now, let’s calculate the total costs for both a 4-inch and a 6-inch slab:
For a 4-inch slab:
- Cost of concrete: $1,480.50
- Labor cost: $4,800
- Site preparation cost: $800
- Rebar cost: $135
- Total cost: $7,215.50
For a 6-inch slab:
- Cost of concrete: $2,221.50
- Labor cost: $4,800
- Site preparation cost: $800
- Rebar cost: $135
- Total cost: $7,956.50
2.6. Summary of Estimated Costs
Slab Thickness | Concrete Cost | Labor Cost | Site Prep | Rebar Cost | Total Cost |
---|---|---|---|---|---|
4 inches | $1,480.50 | $4,800 | $800 | $135 | $7,215.50 |
6 inches | $2,221.50 | $4,800 | $800 | $135 | $7,956.50 |
These estimates provide a general idea of the costs involved in pouring a 20×40 concrete slab. To get a more accurate estimate, it is recommended to obtain quotes from local contractors who can assess your specific site conditions and project requirements.
3. Average Cost of Concrete Slabs by Thickness
The thickness of a concrete slab is a critical factor in determining its cost and suitability for various applications. Different thicknesses are appropriate for different uses, and the cost per square foot varies accordingly. Here’s a breakdown of the average costs associated with different slab thicknesses:
3.1. Cost per Square Foot by Thickness
Slab Thickness | Average Price per Square Foot (Without Labor) | Common Uses |
---|---|---|
2 inches | $4 – $6 | Suitable for light-duty applications such as walkways, patios (with minimal foot traffic), and shed floors. |
4 inches | $6 – $8 | Commonly used for residential patios, driveways (for cars), garage floors, and as a base for sheds and workshops. |
6 inches | $8 – $10 | Ideal for heavier applications such as driveways (for trucks and SUVs), heavy machinery bases, and commercial flooring. |
8 inches | $10 – $12 | Used for industrial flooring, foundations for large structures, and areas subject to very heavy loads. Often required for commercial buildings and applications with significant stress. |
3.2. Cost Factors for Different Thicknesses
- Material Costs: The primary driver of cost differences between slab thicknesses is the volume of concrete required. Thicker slabs require more concrete, leading to higher material costs.
- Labor Costs: While the labor cost per square foot may not increase linearly with thickness, thicker slabs can be more challenging to pour and finish, potentially leading to higher labor expenses.
- Reinforcement: Thicker slabs often require more reinforcement, such as additional rebar or thicker wire mesh, which adds to the overall cost.
- Site Preparation: The need for more extensive site preparation may increase with thicker slabs, especially if the underlying soil is unstable or requires significant compaction.
3.3. Cost Considerations for a 20×40 Concrete Slab
To illustrate the cost differences based on thickness, let’s consider a 20×40 concrete slab (800 square feet):
Slab Thickness | Material Cost (800 sq ft) | Estimated Labor Cost | Total Estimated Cost |
---|---|---|---|
2 inches | $3,200 – $4,800 | $3,200 – $4,800 | $6,400 – $9,600 |
4 inches | $4,800 – $6,400 | $4,800 – $6,400 | $9,600 – $12,800 |
6 inches | $6,400 – $8,000 | $6,400 – $8,000 | $12,800 – $16,000 |
8 inches | $8,000 – $9,600 | $8,000 – $9,600 | $16,000 – $19,200 |
3.4. Additional Cost Factors
- Geographic Location: Prices for concrete and labor can vary significantly by region.
- Concrete Mix: The specific concrete mix required for your project can impact the cost. High-strength mixes or those with special additives will be more expensive.
- Finishes: Decorative finishes like stamped concrete or colored concrete will increase the overall cost.
- Permits: The cost of building permits can vary by municipality.
3.5. Best Practices for Cost Optimization
- Accurate Planning: Proper planning can minimize waste and ensure the most efficient use of materials.
- Multiple Quotes: Obtain quotes from several contractors to ensure you are getting a competitive price.
- Consider Timing: Prices for concrete and labor may fluctuate depending on the time of year and demand.
- Value Engineering: Work with your contractor to identify opportunities to reduce costs without compromising quality or durability.
4. Concrete Slab Thickness: Determining the Right Size
The thickness of a concrete slab is a critical factor determining its strength, durability, and suitability for various applications. Selecting the appropriate thickness involves considering several factors, including the intended use of the slab, soil conditions, and expected loads.
4.1. Factors Influencing Concrete Slab Thickness
- Intended Use: The primary factor in determining slab thickness is its intended use. Light-duty applications like patios and walkways require thinner slabs, while heavy-duty applications like driveways and industrial floors require thicker slabs.
- Soil Conditions: The stability and load-bearing capacity of the underlying soil affect the required thickness. Unstable or poorly compacted soil may necessitate a thicker slab to distribute the load more evenly.
- Expected Loads: The weight and frequency of loads the slab will bear are crucial considerations. Slabs intended to support heavy vehicles or machinery need to be thicker than those designed for pedestrian traffic.
- Reinforcement: The presence and type of reinforcement, such as rebar or wire mesh, can influence the required thickness. Reinforced slabs can often be thinner than unreinforced slabs while maintaining adequate strength.
- Local Building Codes: Local building codes often specify minimum thickness requirements for concrete slabs based on their intended use and location.
- Climate: In regions with significant freeze-thaw cycles, thicker slabs may be necessary to prevent cracking and damage from frost heave.
4.2. Recommended Slab Thicknesses for Various Applications
Application | Recommended Thickness | Notes |
---|---|---|
Walkways and Patios | 4 inches | Suitable for pedestrian traffic and light furniture. May require reinforcement in areas with unstable soil. |
Residential Driveways (Cars) | 4-6 inches | A 4-inch slab is typically sufficient for cars, while a 6-inch slab is recommended for heavier vehicles like trucks and SUVs. Reinforcement is highly recommended. |
Garage Floors | 4-6 inches | Similar to driveways, the thickness depends on the weight of the vehicles and equipment stored in the garage. Reinforcement is important to prevent cracking from heavy loads. |
Shed and Workshop Floors | 4-6 inches | Thickness depends on the size and weight of equipment and materials stored in the shed or workshop. Reinforcement is recommended, especially for larger structures. |
Commercial Flooring | 6-8 inches | Commercial applications typically require thicker slabs to withstand heavy foot traffic and equipment loads. Local building codes should be consulted for specific requirements. |
Industrial Flooring | 8+ inches | Industrial floors are subject to extremely heavy loads and require very thick slabs with substantial reinforcement. A structural engineer should be consulted to determine the appropriate thickness and reinforcement strategy. |
Foundation Slabs (Residential) | 4-8 inches | The thickness of a foundation slab depends on the size and type of the structure it supports. A structural engineer should be consulted to ensure the slab meets all applicable building codes and can support the intended loads. |
Foundation Slabs (Commercial) | 8+ inches | Commercial foundations require even thicker slabs to support larger and heavier structures. A structural engineer is essential for designing commercial foundation slabs. |
4.3. Specific Recommendations for a 20×40 Concrete Slab
For a 20×40 concrete slab, the appropriate thickness depends on its intended use:
- Patio or Walkway: A 4-inch slab is generally sufficient for pedestrian traffic and light furniture.
- Residential Driveway: A 6-inch slab is recommended to support the weight of vehicles.
- Garage Floor: A 6-inch slab is also recommended for garage floors, especially if you plan to store heavy equipment or vehicles.
- Shed or Workshop: A 4-6 inch slab can be used depending on what will be stored within the shed or workshop.
4.4. The Importance of Reinforcement
Reinforcement, typically in the form of rebar or wire mesh, plays a crucial role in enhancing the strength and durability of concrete slabs. Reinforcement helps to distribute loads, prevent cracking, and increase the slab’s resistance to stress.
- Rebar: Rebar is commonly used in thicker slabs and applications requiring high load-bearing capacity.
- Wire Mesh: Wire mesh is often used in thinner slabs to provide additional support and prevent cracking.
4.5. Consulting with Professionals
Determining the appropriate thickness for a concrete slab can be complex, and it’s often best to consult with a structural engineer or experienced concrete contractor. These professionals can assess your specific site conditions, intended use, and local building codes to recommend the optimal thickness and reinforcement strategy.
5. Concrete Slab Volume: Bags vs. Truck Delivery
When planning a concrete slab project, one of the key decisions is whether to mix the concrete yourself using bags or to order a ready-mix concrete truck. The choice depends on the size of the project, your budget, and your physical capabilities.
5.1. Calculating Concrete Volume for a 20×40 Slab
Before deciding between bags and a truck, it’s essential to calculate the total volume of concrete needed for your slab. As discussed earlier, the volume depends on the dimensions and thickness of the slab.
For a 20×40 slab:
- 4-inch slab: Requires approximately 9.87 cubic yards of concrete.
- 6-inch slab: Requires approximately 14.81 cubic yards of concrete.
5.2. Using Concrete Bags: Advantages and Disadvantages
Advantages:
- Flexibility: Bags allow you to mix concrete in smaller batches, providing greater control over the mixing process.
- Portability: Bags are easy to transport, especially for projects in hard-to-reach areas.
- Lower Initial Cost: For very small projects, buying bags may be cheaper than ordering a truck.
Disadvantages:
- Labor-Intensive: Mixing concrete by hand or with a small mixer is physically demanding and time-consuming.
- Inconsistent Mix: Achieving a consistent mix with bags can be challenging, especially for large projects.
- Higher Overall Cost: For larger projects, the cost of buying and mixing numerous bags of concrete can exceed the cost of ordering a truck.
- Time-Consuming: Manually mixing hundreds of bags takes significantly longer than pouring from a concrete truck.
5.3. Ordering a Concrete Truck: Advantages and Disadvantages
Advantages:
- Convenience: A concrete truck delivers a large volume of ready-mix concrete directly to your site, saving you time and effort.
- Consistency: Ready-mix concrete is produced in a controlled environment, ensuring a consistent mix and quality.
- Cost-Effective: For medium to large projects, ordering a truck is typically more cost-effective than buying and mixing bags of concrete.
- Speed: A concrete truck can pour a large slab much faster than you could mix and pour using bags.
Disadvantages:
- Higher Initial Cost: Ordering a concrete truck typically has a higher upfront cost than buying bags.
- Accessibility: Trucks require clear access to the pour site, which may be a challenge in some locations.
- Minimum Order Quantities: Concrete suppliers may have minimum order quantities, which could be more than you need for a small project.
- Timing: You need to coordinate the delivery of the truck with your schedule and ensure you have enough labor to pour the concrete quickly.
5.4. Calculating the Number of Bags Needed
If you decide to use concrete bags, you’ll need to calculate how many bags you need based on the volume of concrete required.
-
Typical Bag Sizes: Concrete bags come in various sizes, typically ranging from 40 to 80 pounds. An 80-pound bag of concrete mix typically yields about 0.6 cubic feet of concrete.
-
Calculating the Number of Bags:
- Convert the total volume of concrete needed from cubic yards to cubic feet (1 cubic yard = 27 cubic feet).
- Divide the total volume in cubic feet by the yield per bag (0.6 cubic feet for an 80-pound bag) to determine the number of bags needed.
For a 4-inch slab (9.87 cubic yards):
- Total volume in cubic feet = 9.87 cubic yards x 27 cubic feet/yard = 266.49 cubic feet
- Number of 80-pound bags needed = 266.49 cubic feet / 0.6 cubic feet/bag = Approximately 444 bags
5.5. Making the Decision: Bags or Truck?
For a 20×40 concrete slab, which requires a significant volume of concrete, ordering a concrete truck is generally the better option. The advantages of convenience, consistency, and cost-effectiveness outweigh the higher initial cost.
However, if you have limited access to the site, a small budget, and plenty of time and labor, using bags may be feasible. Just be prepared for the physical demands and potential inconsistencies in the mix.
6. Cubic Yards of Concrete for a 20×40 Slab: Accurate Estimates
Accurately estimating the amount of concrete needed for a 20×40 slab is crucial for budgeting and ensuring you have enough material to complete the project. This section provides a detailed guide on calculating the required cubic yards of concrete, considering different slab thicknesses.
6.1. Basic Formula for Calculating Concrete Volume
The basic formula for calculating the volume of concrete needed is:
Volume = Length x Width x Thickness
6.2. Converting Measurements to Consistent Units
Before applying the formula, it’s essential to ensure all measurements are in the same units. Typically, concrete slab dimensions are given in feet, while thickness is often specified in inches. To maintain consistency, convert the thickness from inches to feet.
- 1 foot = 12 inches
- Thickness in feet = Thickness in inches / 12
6.3. Calculating Concrete Volume for Different Slab Thicknesses
Let’s calculate the concrete volume for a 20×40 slab with thicknesses of 4 inches and 6 inches:
For a 4-inch Slab:
-
Convert thickness to feet:
- 4 inches = 4/12 feet = 0.333 feet
-
Calculate volume in cubic feet:
- Volume = Length x Width x Thickness
- Volume = 40 feet x 20 feet x 0.333 feet = 266.4 cubic feet
-
Convert cubic feet to cubic yards:
- 1 cubic yard = 27 cubic feet
- Cubic yards = Volume in cubic feet / 27
- Cubic yards = 266.4 cubic feet / 27 cubic feet/yard ≈ 9.87 cubic yards
For a 6-inch Slab:
-
Convert thickness to feet:
- 6 inches = 6/12 feet = 0.5 feet
-
Calculate volume in cubic feet:
- Volume = Length x Width x Thickness
- Volume = 40 feet x 20 feet x 0.5 feet = 400 cubic feet
-
Convert cubic feet to cubic yards:
- 1 cubic yard = 27 cubic feet
- Cubic yards = Volume in cubic feet / 27
- Cubic yards = 400 cubic feet / 27 cubic feet/yard ≈ 14.81 cubic yards
6.4. Accounting for Waste and Overages
In practice, it’s wise to order slightly more concrete than the calculated volume to account for waste, spillage, uneven surfaces, and potential variations in thickness. A common rule of thumb is to add 5-10% to the calculated volume.
For a 4-inch Slab:
- Calculated volume: 9.87 cubic yards
- 5% overage: 9.87 x 0.05 = 0.49 cubic yards
- Total volume to order: 9.87 + 0.49 ≈ 10.36 cubic yards
For a 6-inch Slab:
- Calculated volume: 14.81 cubic yards
- 5% overage: 14.81 x 0.05 = 0.74 cubic yards
- Total volume to order: 14.81 + 0.74 ≈ 15.55 cubic yards
6.5. Summary of Concrete Volume Estimates
Slab Thickness | Calculated Volume (Cubic Yards) | Recommended Overage (5%) | Total Volume to Order (Cubic Yards) |
---|---|---|---|
4 inches | 9.87 | 0.49 | 10.36 |
6 inches | 14.81 | 0.74 | 15.55 |
6.6. Additional Considerations
- Soil Conditions: Uneven or poorly compacted soil may require additional concrete to fill voids, increasing the overall volume needed.
- Formwork: Ensure your formwork is properly constructed and sealed to prevent concrete from leaking out, which can lead to waste.
- Concrete Supplier: Consult with your concrete supplier to confirm their minimum order quantities and delivery options.
6.7. Why Accurate Estimates Matter
Accurate concrete volume estimates are essential for:
- Budgeting: Avoiding cost overruns by ordering the right amount of concrete.
- Project Efficiency: Minimizing delays by having enough concrete on hand to complete the pour in one go.
- Waste Reduction: Preventing unnecessary waste of concrete, which is both environmentally and economically beneficial.
7. Rebar Requirements for a 20×40 Slab: A Detailed Guide
Reinforcing concrete slabs with rebar (reinforcement bar) is crucial for increasing their strength and durability, particularly in applications subject to heavy loads or unstable soil conditions. This section provides a comprehensive guide to calculating the rebar requirements for a 20×40 concrete slab.
7.1. Understanding the Role of Rebar
Rebar enhances the tensile strength of concrete, which is naturally strong in compression but weak in tension. By embedding rebar within the concrete, you create a composite material that can withstand greater loads and resist cracking.
7.2. Factors Influencing Rebar Requirements
- Intended Use: The primary factor is the intended use of the slab. Heavy-duty applications like driveways and industrial floors require more rebar than light-duty applications like patios and walkways.
- Slab Thickness: Thicker slabs generally require more rebar to provide adequate reinforcement.
- Soil Conditions: Unstable or expansive soil may necessitate additional rebar to prevent cracking and movement.
- Expected Loads: The weight and frequency of loads the slab will bear are crucial considerations.
- Local Building Codes: Local building codes often specify minimum rebar requirements based on the intended use and location of the slab.
- Rebar Spacing: The spacing between rebar grids affects the overall strength and load-bearing capacity of the slab. Closer spacing provides greater reinforcement.
7.3. Calculating Rebar Requirements for a 20×40 Slab
For a 20×40 slab, a common approach is to create a grid of rebar spaced at regular intervals. Here’s how to calculate the rebar requirements:
-
Determine Rebar Spacing:
- A typical rebar spacing for residential slabs is 12-18 inches. For this calculation, we’ll use a spacing of 18 inches.
-
Calculate the Number of Rebar Lengthwise:
- Slab length: 40 feet = 480 inches
- Number of rebars = Slab length / Spacing
- Number of rebars = 480 inches / 18 inches ≈ 27 rebars
-
Calculate the Number of Rebar Widthwise:
- Slab width: 20 feet = 240 inches
- Number of rebars = Slab width / Spacing
- Number of rebars = 240 inches / 18 inches ≈ 14 rebars
-
Calculate the Length of Each Rebar:
- Lengthwise rebars: Each rebar spans the width of the slab (20 feet)
- Widthwise rebars: Each rebar spans the length of the slab (40 feet)
-
Calculate the Total Length of Rebar Needed:
- Total length of lengthwise rebars = Number of rebars x Length of each rebar
- Total length of lengthwise rebars = 27 rebars x 20 feet/rebar = 540 feet
- Total length of widthwise rebars = Number of rebars x Length of each rebar
- Total length of widthwise rebars = 14 rebars x 40 feet/rebar = 560 feet
- Total rebar length = Total length of lengthwise rebars + Total length of widthwise rebars
- Total rebar length = 540 feet + 560 feet = 1100 feet
-
Account for Overlap and Wastage:
- Rebar needs to overlap at splices to ensure continuity. A common practice is to add 10-15% extra length for overlaps and wastage.
- Additional rebar (10%): 1100 feet x 0.10 = 110 feet
- Total rebar length with overlap = 1100 feet + 110 feet = 1210 feet
7.4. Summary of Rebar Requirements
Dimension | Value |
---|---|
Slab Length | 40 feet (480 inches) |
Slab Width | 20 feet (240 inches) |
Rebar Spacing | 18 inches |
Number of Lengthwise Rebars | 27 |
Number of Widthwise Rebars | 14 |
Length of Each Lengthwise Rebar | 20 feet |
Length of Each Widthwise Rebar | 40 feet |
Total Rebar Length (Without Overlap) | 1100 feet |
Total Rebar Length (With 10% Overlap) | 1210 feet |
7.5. Additional Considerations
- Rebar Size: The appropriate rebar size depends on the expected loads and local building codes. Common sizes include #3 (3/8 inch diameter) and #4 (1/2 inch diameter).
- Rebar Placement: Ensure the rebar is properly positioned within the slab, typically in the middle third of the concrete thickness.
- Support Chairs: Use support chairs to hold the rebar in place during the pour, ensuring it remains at the correct height.
- Professional Consultation: Consult with a structural engineer or experienced concrete contractor to confirm the appropriate rebar requirements for your specific project.
7.6. Skipping the Math with a Rebar Calculator
For those who prefer to skip the manual calculations, there are online rebar calculators available that can provide estimates based on your slab dimensions and intended use.
By following this detailed guide, you can accurately estimate the rebar requirements for your 20×40 concrete slab, ensuring a strong and durable foundation for your project.
8. Need Expert Advice on Your Concrete Slab Project?
Planning a concrete slab project can be complex, with numerous factors influencing the final cost and quality. From determining the right thickness and reinforcement to calculating the precise amount of concrete needed, making informed decisions is crucial for success.
At how.edu.vn, we connect you with leading Ph.D. experts who can provide personalized guidance and support for your concrete slab project. Our team of experienced professionals can help you:
- Accurately estimate costs: Get a detailed breakdown of all expenses, including materials, labor, site preparation, and permits.
- Determine the optimal slab thickness and reinforcement: Ensure your slab is strong and durable enough to meet your specific needs.
- Choose the right concrete mix: Select the best mix for your application, considering factors like strength, durability, and climate.
- Navigate local building codes and regulations: Ensure your project complies with all applicable requirements.
- Find qualified contractors: Get recommendations for reputable