How Much Is Carbon Fiber, and how does it benefit various industries? At HOW.EDU.VN, we break down the carbon fiber cost, exploring its raw materials, energy requirements, production processes, and technological advancements influencing its price. Discover how you can access expert advice to optimize your material choices. Learn about the factors driving cost reductions and explore insights into related materials and innovative composites.
1. Understanding the Raw Materials Affecting Carbon Fiber Cost
Carbon fiber, celebrated for its unparalleled strength-to-weight ratio, is a composite material crafted from multiple components. The cost of these base products significantly influences the final price of carbon fiber. The primary raw materials include:
- Polyacrylonitrile (PAN): The most common precursor, accounting for about 90% of carbon fiber production. Its quality and availability directly impact the cost.
- Rayon: An alternative precursor, especially for specialty applications. While less common, it can affect the overall cost depending on market conditions.
- Pitch: Derived from petroleum or coal, pitch is used in lower-cost carbon fibers. Its availability and processing requirements also play a role in the price.
Understanding the composition of PAN, rayon, and pitch in carbon fiber production and their impact on overall material costs.
Material | Impact on Cost |
---|---|
Polyacrylonitrile | Dominant material; fluctuations in its market price significantly affect carbon fiber cost. |
Rayon | Used in niche applications; cost varies with market demand and specialty processing. |
Pitch | Lower-cost alternative; pricing depends on petroleum and coal market dynamics. |
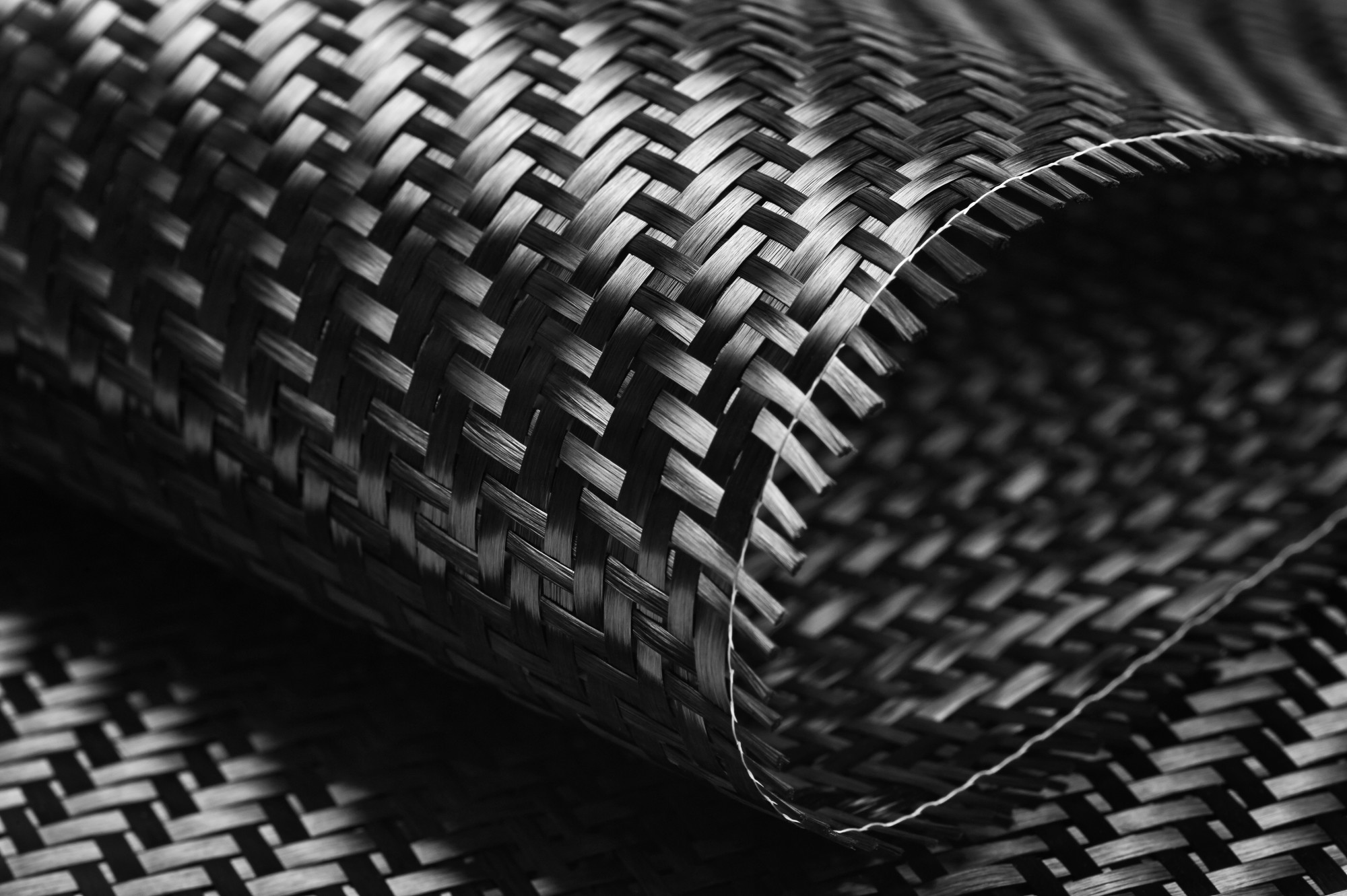
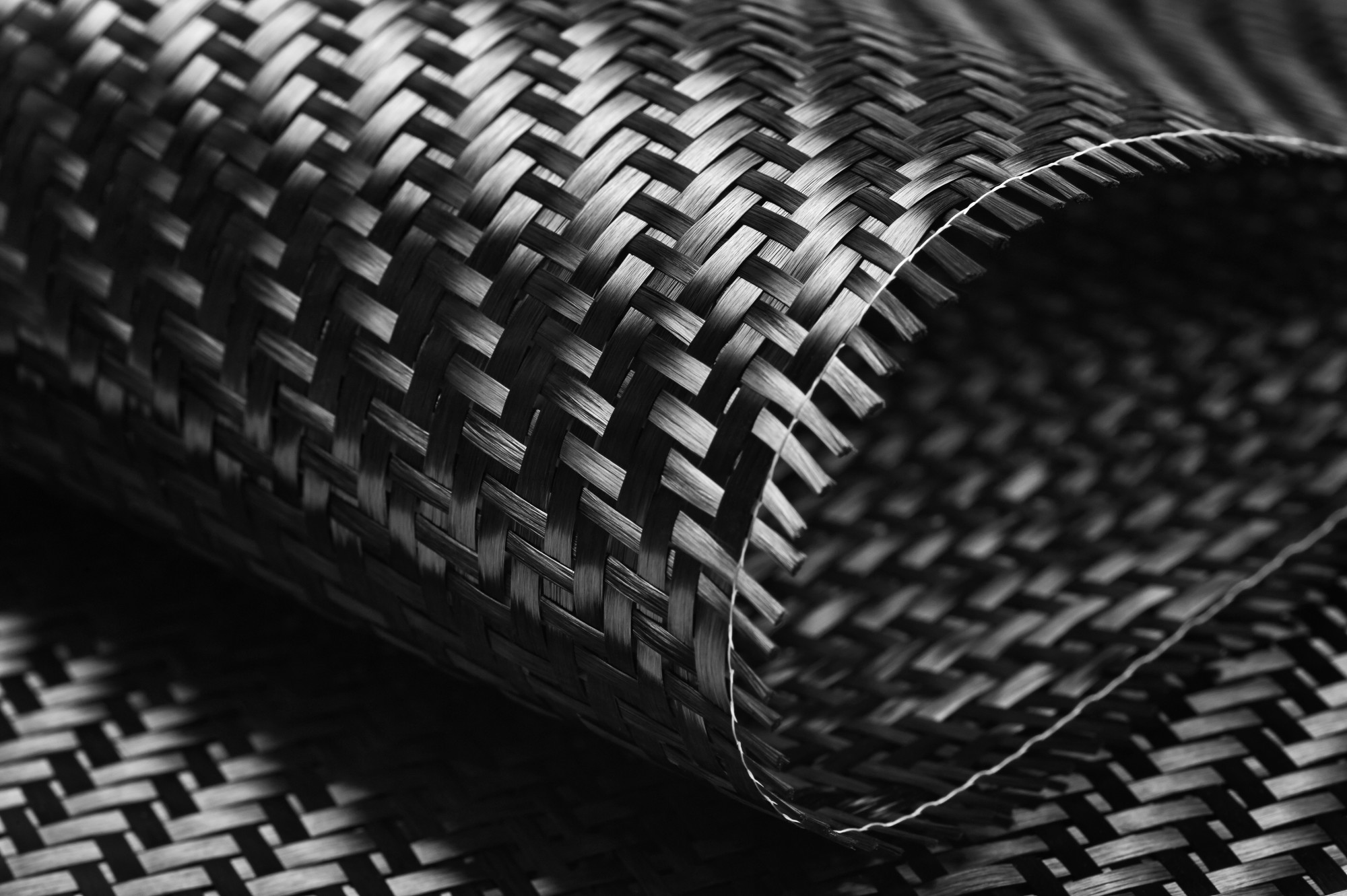
Researchers are continually exploring innovative methods and alternative raw materials to mitigate carbon fiber costs. For instance, developing more reactive resins reduces the processing time, resulting in significant savings. If you’re facing challenges in material selection or cost optimization, HOW.EDU.VN provides direct access to expert consultants who can guide you toward efficient and economical solutions. Connect with our specialists to explore how alternative materials and innovative manufacturing techniques can benefit your projects. Our team of over 100 Ph.D. level experts is ready to provide tailored advice and help you navigate the complexities of material costs.
2. The Significant Role of Energy in Carbon Fiber Production Expenses
Energy consumption is a pivotal factor in determining the overall cost of carbon fiber. After creating resin fibers from precursors like PAN, manufacturers subject these fibers to chemical treatments, heat, and stretching. This process, known as carbonization, reinforces the fibers with carbon atoms. The energy-intensive nature of this process is a primary driver of manufacturing expenses. Securing affordable and reliable energy sources is essential for cost-effective carbon fiber production. Energy costs are not just about the price per unit but also include the expenses associated with equipment maintenance and energy infrastructure.
Energy Source | Cost Implications |
---|---|
Electricity | High consumption during carbonization; costs depend on regional electricity rates. |
Natural Gas | Used for heating processes; price volatility affects overall production costs. |
Renewable Energy | Offers long-term cost stability but requires significant upfront investment. |
Manufacturers are increasingly adopting energy-efficient technologies and renewable energy sources to mitigate these costs. Innovations in carbon fiber production include reducing process cycle times, enhancing heating efficiency, and developing methods that require less energy input. For example, companies are exploring microwave heating and plasma treatments to accelerate carbonization while using less energy. These efforts not only reduce costs but also enhance the environmental sustainability of carbon fiber production. Do you need help assessing the energy efficiency of your manufacturing process or identifying cost-saving opportunities? At HOW.EDU.VN, our expert consultants specialize in optimizing industrial processes for maximum efficiency and cost-effectiveness. Contact our team today to discover how you can improve your energy usage and reduce your carbon fiber production costs.
3. Production Processes and Their Impact on Carbon Fiber Pricing
The production phase of carbon fiber manufacturing involves multiple complex processes that contribute significantly to the final cost. Key elements include labor, specialized machinery, and process optimization, all of which require substantial investment and expertise. Labor costs are substantial, as manufacturing carbon fiber demands a highly skilled workforce capable of managing intricate machinery and processes. These specialists must be adept at monitoring quality control, maintaining equipment, and troubleshooting issues that arise during production. The complexity of carbon fiber manufacturing necessitates extensive training and ongoing education for workers, adding to the overall labor expenses. Specialized machinery, such as fiber spinning machines, oxidation ovens, and carbonization furnaces, represents a considerable capital investment. These machines often require precise calibration and regular maintenance to ensure optimal performance. The cost of replacement parts, repairs, and upgrades further contributes to the financial burden.
Depicts the advanced machinery used in the production of carbon fiber, emphasizing the high-tech nature of labor and equipment required.
Process | Cost Drivers |
---|---|
Fiber Spinning | High-precision machinery, skilled operators, quality control measures. |
Oxidation | Energy-intensive heating, precise temperature control, long cycle times. |
Carbonization | High energy consumption, specialized furnaces, atmosphere control. |
Surface Treatment | Chemical treatments, equipment maintenance, environmental compliance. |
Sizing | Application of protective coatings, quality inspection, material waste management. |
Process optimization is crucial for reducing production costs. Manufacturers continually seek ways to streamline their operations, improve material handling, and minimize waste. Advances in automation, such as robotic systems for material transfer and automated quality inspection, can significantly reduce labor costs and improve production efficiency. However, the initial investment in these technologies can be substantial. Are you struggling with high production costs or looking for ways to streamline your manufacturing processes? HOW.EDU.VN provides access to top-tier consultants who specialize in manufacturing optimization. Our experts can help you identify inefficiencies, implement cost-saving strategies, and leverage cutting-edge technologies to improve your bottom line. Contact our team today to schedule a consultation and take the first step toward more efficient and cost-effective carbon fiber production.
4. The Role of Software and Technology in Reducing Carbon Fiber Costs
In addition to manufacturing and assembly machinery, software and technology play a vital role in reducing carbon fiber costs. Advanced software solutions streamline various aspects of the manufacturing process, including design, simulation, cost modeling, and risk management. Sophisticated design simulation software significantly reduces the design cycle time. By allowing engineers to virtually test and refine designs, these tools minimize the need for physical prototypes, saving time and resources. Simulation software can also optimize the use of materials and identify potential design flaws early in the process, preventing costly rework later on. Cost modeling software offers a comprehensive analysis of efficiency losses. These tools help manufacturers identify bottlenecks, waste, and other inefficiencies in their production processes. By providing detailed insights into cost drivers, cost modeling software enables companies to make data-driven decisions that improve resource allocation and reduce overall expenses.
Software Type | Benefits |
---|---|
Design Simulation | Reduces design cycle time, optimizes material use, identifies design flaws early. |
Cost Modeling | Analyzes efficiency losses, identifies cost drivers, improves resource allocation. |
Knowledge-Based Systems | Lowers labor costs, captures and reuses expert knowledge, improves decision-making. |
Risk Management | Identifies manufacturing risks upfront, prevents costly mistakes, reduces cycle times. |
Knowledge-based engineering products lower labor costs by capturing and reusing expert knowledge. These systems provide workers with access to best practices, standard operating procedures, and troubleshooting guides, reducing the need for highly skilled personnel in every role. By democratizing knowledge, companies can improve productivity and reduce training costs. Moreover, software providers are introducing products that help identify manufacturing risks upfront. These risk management tools use predictive analytics and machine learning to anticipate potential problems and prevent costly mistakes before they occur. By identifying risks early, companies can take proactive measures to mitigate them, reducing cycle times and minimizing waste. Are you looking to leverage software and technology to reduce your carbon fiber costs? At HOW.EDU.VN, our expert consultants specialize in helping companies implement cutting-edge technologies to optimize their manufacturing processes. Contact our team today to learn how you can harness the power of software to improve efficiency and reduce costs.
5. Addressing the Intended Searches of Users Regarding Carbon Fiber Costs
Understanding the various intentions behind user searches for carbon fiber costs is crucial for providing relevant and comprehensive information. Here are five common user search intents and how to address them:
- Information on the Current Market Price:
- Users want to know the current price range of carbon fiber per pound or meter.
- Address by providing up-to-date market prices, citing reputable sources, and explaining the factors that influence these prices, such as grade, quantity, and supplier.
- Comparison with Other Materials:
- Users are comparing the cost of carbon fiber with alternative materials like aluminum, steel, or fiberglass.
- Address by offering a detailed cost comparison, highlighting the advantages and disadvantages of each material in terms of performance, durability, and application-specific suitability.
- Understanding Cost Factors:
- Users want to understand what contributes to the cost of carbon fiber, including raw materials, manufacturing processes, and technology.
- Address by breaking down the cost components, explaining each factor’s impact on the final price, and discussing how advancements in technology and manufacturing can reduce costs.
- Finding Cost-Effective Suppliers:
- Users are looking for suppliers who offer competitive prices without compromising quality.
- Address by providing guidance on how to evaluate suppliers, negotiate prices, and assess the quality of carbon fiber. Offer tips on identifying reputable suppliers and avoiding common pitfalls.
- Application-Specific Cost Analysis:
- Users need to understand the cost implications of using carbon fiber in specific applications, such as automotive, aerospace, or sporting goods.
- Address by providing case studies or examples of how carbon fiber is used in different industries, detailing the cost benefits and trade-offs compared to traditional materials. At HOW.EDU.VN, our consultants are adept at addressing these diverse search intents, providing tailored advice and comprehensive solutions to meet your specific needs. Whether you need help with market analysis, material selection, or supply chain optimization, our experts are here to guide you.
6. Optimizing Carbon Fiber Usage in Automotive Engineering
In automotive engineering, carbon fiber’s lightweight and high-strength properties offer significant advantages. However, the cost of carbon fiber can be a barrier. Optimizing its use involves strategic application in critical areas such as body panels, chassis components, and interior structures. Cost-saving strategies include:
- Hybrid Material Designs: Combining carbon fiber with less expensive materials like aluminum or high-strength steel to reduce overall costs while maintaining performance.
- Localized Reinforcement: Using carbon fiber only in areas requiring high strength and stiffness, rather than throughout the entire structure.
- Standardized Parts: Designing standardized carbon fiber components that can be used across multiple vehicle models to increase production volume and lower unit costs.
- Automation in Manufacturing: Implementing automated processes for cutting, shaping, and assembling carbon fiber parts to reduce labor costs and improve production efficiency.
- Recycling and Reuse: Developing methods for recycling carbon fiber waste and end-of-life components to reduce material costs and environmental impact.
Strategy | Cost Impact |
---|---|
Hybrid Material Designs | Reduces material costs by combining carbon fiber with cheaper alternatives. |
Localized Reinforcement | Minimizes the amount of carbon fiber needed, focusing on critical areas. |
Standardized Parts | Increases production volume, lowering unit costs through economies of scale. |
Automation in Manufacturing | Reduces labor costs, improves production efficiency, and minimizes waste. |
Recycling and Reuse | Lowers material costs, reduces environmental impact, and promotes sustainability. |
For instance, BMW’s i3 electric car uses a carbon fiber reinforced plastic (CFRP) passenger cell to reduce weight and improve energy efficiency. This demonstrates how strategic use of carbon fiber can enhance vehicle performance while managing costs. Are you looking to optimize the use of carbon fiber in your automotive designs? At HOW.EDU.VN, our consultants specialize in material selection, design optimization, and manufacturing process improvement. Contact our team today to discover how you can leverage carbon fiber to enhance vehicle performance while minimizing costs.
7. Maximizing Benefits of Carbon Fiber in Aerospace Applications
In aerospace, carbon fiber composites are essential for reducing aircraft weight, improving fuel efficiency, and enhancing structural integrity. However, the high cost of carbon fiber demands strategic implementation. Optimization strategies include:
- Advanced Composite Design: Utilizing advanced design techniques to maximize the structural efficiency of carbon fiber components, reducing the amount of material needed.
- Automated Fiber Placement: Employing automated fiber placement (AFP) and automated tape laying (ATL) technologies to precisely align carbon fibers, minimizing waste and improving structural performance.
- Out-of-Autoclave Processing: Using out-of-autoclave (OOA) curing methods to reduce manufacturing costs and cycle times, as these methods do not require expensive autoclaves.
- Integrated Structures: Designing integrated structures that combine multiple components into a single carbon fiber part, reducing assembly costs and improving structural integrity.
- Lifecycle Cost Analysis: Conducting thorough lifecycle cost analyses to assess the long-term benefits of using carbon fiber, including reduced fuel consumption and maintenance costs.
Strategy | Benefit |
---|---|
Advanced Composite Design | Reduces material usage, optimizes structural performance, and minimizes weight. |
Automated Fiber Placement | Minimizes waste, improves fiber alignment, and enhances structural integrity. |
Out-of-Autoclave Processing | Reduces manufacturing costs, shortens cycle times, and eliminates the need for autoclaves. |
Integrated Structures | Lowers assembly costs, improves structural integrity, and reduces part count. |
Lifecycle Cost Analysis | Provides a comprehensive assessment of long-term cost benefits. |
For example, Boeing’s 787 Dreamliner incorporates significant amounts of carbon fiber composites in its fuselage and wings, resulting in a lighter, more fuel-efficient aircraft. This illustrates how strategic use of carbon fiber can provide substantial long-term cost savings in aerospace applications. Are you looking to maximize the benefits of carbon fiber in your aerospace designs? At HOW.EDU.VN, our consultants specialize in aerospace engineering, composite materials, and manufacturing process optimization. Contact our team today to discover how you can leverage carbon fiber to improve aircraft performance while minimizing costs.
8. Applying Carbon Fiber Composites Effectively in Sporting Goods
In the sporting goods industry, carbon fiber composites are used to enhance the performance of equipment such as bicycles, golf clubs, tennis rackets, and hockey sticks. The lightweight and high-strength properties of carbon fiber allow athletes to achieve better results. Effective application strategies include:
- Targeted Reinforcement: Reinforcing specific areas of sporting goods equipment with carbon fiber to improve stiffness and strength where it is needed most.
- Hybrid Composites: Combining carbon fiber with other materials, such as fiberglass or polymers, to balance performance and cost.
- Optimized Layup: Carefully designing the layup of carbon fiber layers to maximize strength and stiffness while minimizing weight.
- Customization: Tailoring the properties of carbon fiber composites to meet the specific needs of different athletes and sports.
- Ergonomic Design: Using carbon fiber composites to create ergonomically designed sporting goods that enhance comfort and performance.
Strategy | Application |
---|---|
Targeted Reinforcement | Improves stiffness and strength in specific areas of bicycles, golf clubs, and tennis rackets. |
Hybrid Composites | Balances performance and cost in hockey sticks, baseball bats, and fishing rods. |
Optimized Layup | Maximizes strength and stiffness while minimizing weight in skis and snowboards. |
Customization | Tailors properties to meet the needs of different athletes and sports in racing bikes. |
Ergonomic Design | Enhances comfort and performance in golf clubs and rowing oars. |
For instance, high-end bicycles use carbon fiber frames to reduce weight and improve stiffness, resulting in a faster and more responsive ride. Similarly, golf clubs with carbon fiber shafts provide increased swing speed and distance. Are you looking to apply carbon fiber composites effectively in your sporting goods products? At HOW.EDU.VN, our consultants specialize in materials engineering, product design, and manufacturing process optimization. Contact our team today to discover how you can leverage carbon fiber to enhance the performance and market appeal of your sporting goods.
9. Future Trends in Carbon Fiber Production and Cost Reduction
The future of carbon fiber production is geared towards reducing costs, enhancing sustainability, and improving performance. Key trends include:
- Bio-Based Precursors: Developing carbon fiber from renewable bio-based precursors such as lignin and cellulose to reduce reliance on petroleum-based materials.
- Advanced Recycling Technologies: Implementing advanced recycling technologies to recover and reuse carbon fiber from waste and end-of-life products, reducing material costs and environmental impact.
- Nanomaterial Integration: Integrating nanomaterials such as carbon nanotubes and graphene into carbon fiber composites to enhance strength, stiffness, and conductivity.
- Digital Manufacturing: Utilizing digital manufacturing technologies such as 3D printing and simulation to optimize the design and production of carbon fiber components.
- Smart Composites: Developing smart composites with embedded sensors and actuators to monitor structural health and performance in real-time.
Trend | Impact |
---|---|
Bio-Based Precursors | Reduces reliance on petroleum-based materials, promotes sustainability, and lowers costs. |
Advanced Recycling | Recovers and reuses carbon fiber, reduces waste, and lowers material costs. |
Nanomaterial Integration | Enhances strength, stiffness, conductivity, and functionality of composites. |
Digital Manufacturing | Optimizes design and production, reduces waste, and lowers manufacturing costs. |
Smart Composites | Monitors structural health, improves performance, and enhances safety. |
For example, researchers are exploring the use of lignin, a byproduct of the paper industry, as a sustainable and low-cost precursor for carbon fiber production. This could significantly reduce the environmental impact and cost of carbon fiber. Are you looking to stay ahead of the curve in carbon fiber production and cost reduction? At HOW.EDU.VN, our consultants specialize in materials science, nanotechnology, and sustainable manufacturing. Contact our team today to discover how you can leverage these emerging trends to improve your products and processes.
10. Maximizing Cost-Effectiveness with Expert Carbon Fiber Consultation
Navigating the complexities of carbon fiber costs and applications requires expertise and strategic planning. Consulting with experts offers numerous benefits:
- In-Depth Knowledge: Access to professionals with deep knowledge of carbon fiber materials, manufacturing processes, and cost drivers.
- Tailored Solutions: Customized strategies to optimize the use of carbon fiber in your specific applications, considering performance requirements and budget constraints.
- Cost-Saving Opportunities: Identification of cost-saving opportunities through material selection, design optimization, and process improvement.
- Risk Mitigation: Mitigation of risks associated with carbon fiber adoption, such as material defects, manufacturing challenges, and supply chain disruptions.
- Competitive Advantage: Gaining a competitive advantage by leveraging the unique properties of carbon fiber to enhance product performance and reduce costs.
Benefit | Description |
---|---|
In-Depth Knowledge | Access to professionals with expertise in carbon fiber materials and manufacturing. |
Tailored Solutions | Customized strategies to optimize carbon fiber use in specific applications. |
Cost-Saving Opportunities | Identification of opportunities to reduce costs through material selection and process optimization. |
Risk Mitigation | Mitigation of risks associated with carbon fiber adoption and manufacturing. |
Competitive Advantage | Gaining an edge by leveraging carbon fiber to enhance product performance. |
By consulting with experts at HOW.EDU.VN, you can make informed decisions about carbon fiber adoption, optimize its use in your products, and achieve significant cost savings. Our team of over 100 Ph.D. level experts is ready to provide tailored advice and help you navigate the complexities of carbon fiber technology.
FAQ: Carbon Fiber Costs and Applications
- What is the current average cost of carbon fiber per pound?
- The cost varies depending on the grade and quantity, but industrial-grade carbon fiber typically ranges from $7 to $15 per pound.
- How does carbon fiber compare in cost to aluminum or steel?
- Carbon fiber is generally more expensive than aluminum or steel, but its superior strength-to-weight ratio can justify the higher cost in certain applications.
- What are the main factors that influence the cost of carbon fiber?
- Raw materials, energy consumption, manufacturing processes, and technology investments are key factors.
- Can recycling reduce the cost of carbon fiber?
- Yes, advanced recycling technologies can recover and reuse carbon fiber, reducing material costs and environmental impact.
- How can I find cost-effective carbon fiber suppliers?
- Evaluate suppliers based on price, quality, reliability, and technical support. Negotiate prices and assess the quality of carbon fiber samples before committing to a large order.
- Is it possible to combine carbon fiber with cheaper materials to reduce costs?
- Yes, hybrid material designs can combine carbon fiber with less expensive materials like aluminum or fiberglass to balance performance and cost.
- What are the best applications for carbon fiber in the automotive industry?
- Carbon fiber is best used in body panels, chassis components, and interior structures to reduce weight and improve performance.
- How can I optimize the use of carbon fiber in aerospace designs?
- Use advanced composite design techniques, automated fiber placement, and out-of-autoclave processing to maximize structural efficiency and reduce manufacturing costs.
- What are some innovative technologies for reducing carbon fiber production costs?
- Bio-based precursors, nanomaterial integration, digital manufacturing, and smart composites are promising technologies.
- Where can I find expert advice on carbon fiber costs and applications?
- At HOW.EDU.VN, our consultants specialize in carbon fiber materials, manufacturing processes, and cost optimization. Contact our team today for tailored advice and comprehensive solutions.
Are you seeking expert advice on carbon fiber costs and applications? Don’t navigate these complexities alone. HOW.EDU.VN connects you directly with over 100 Ph.D. level experts ready to provide personalized guidance. We understand the challenges in finding qualified professionals and the importance of reliable, actionable advice.
Take the Next Step:
- Contact us: Reach out via WhatsApp at +1 (310) 555-1212 or visit our website at HOW.EDU.VN to schedule a consultation.
- Visit us: Our office is located at 456 Expertise Plaza, Consult City, CA 90210, United States.
Let how.edu.vn be your partner in achieving cost-effective and high-performance carbon fiber solutions. Your success is our priority.